Manufacturing History
The diesel locomotive pioneer revolutionized the railroad industry.
EMD Turns 100
This is the largest and most powerful diesel-electric locomotive ever made in the United States. The dual-engine behemoth, which generated 6,600-hp, was made for Union Pacific in the late 1960s. Photo courtesy Preston Cook
For decades, General Motors was king of the highway and queen of the rails. In addition to mass-producing buses, cars and trucks, the automaker was once the largest locomotive builder in the world. At a massive factory just west of Chicago, GM’s Electro-Motive Division (EMD) assembled powerful machines that helped transition American railroads from steam to diesel.
EMD, which still exists today as Progress Rail Services Corp., a division of Caterpillar Inc., recently celebrated its centennial. The company traces its roots to Cleveland, where the Electro-Motive Engineering Corp. was established in 1922 to design gasoline engine powered, electric-motor driven railcars for light-duty passenger service.
The firm quickly changed its name to Electro-Motive Co. (EMC), but didn’t operate a factory. Instead, it purchased components from suppliers, such as General Electric Co. and Winton Engine Co., and contracted with St. Louis Car Co., Standard Steel Car Co. and other builders to assemble its products.
General Motors Corp. purchased EMC in 1930 and began developing diesel-electric locomotives. A few years later, EMC changed its name to EMD. In 1936, EMD opened a 200,000-square-foot factory in McCook, IL, which was eventually expanded several times as production volume grew.
Chicago was a logical location for the assembly plant, because it was the railroad capital of America. The trend-setting products made inside EMD’s state-of-the-art facility soon dramatically altered the face of railroading.
Evolutionary Period
This 1930s view looking north in the main erecting bay shows a variety of switcher locomotives being assembled with 600-hp diesel engines. The streamlined passenger units in the middle are being built to haul the Union Pacific’s “City of Los Angeles” train, which ran between Chicago and Los Angeles. Photo courtesy Progress Rail Services Inc.
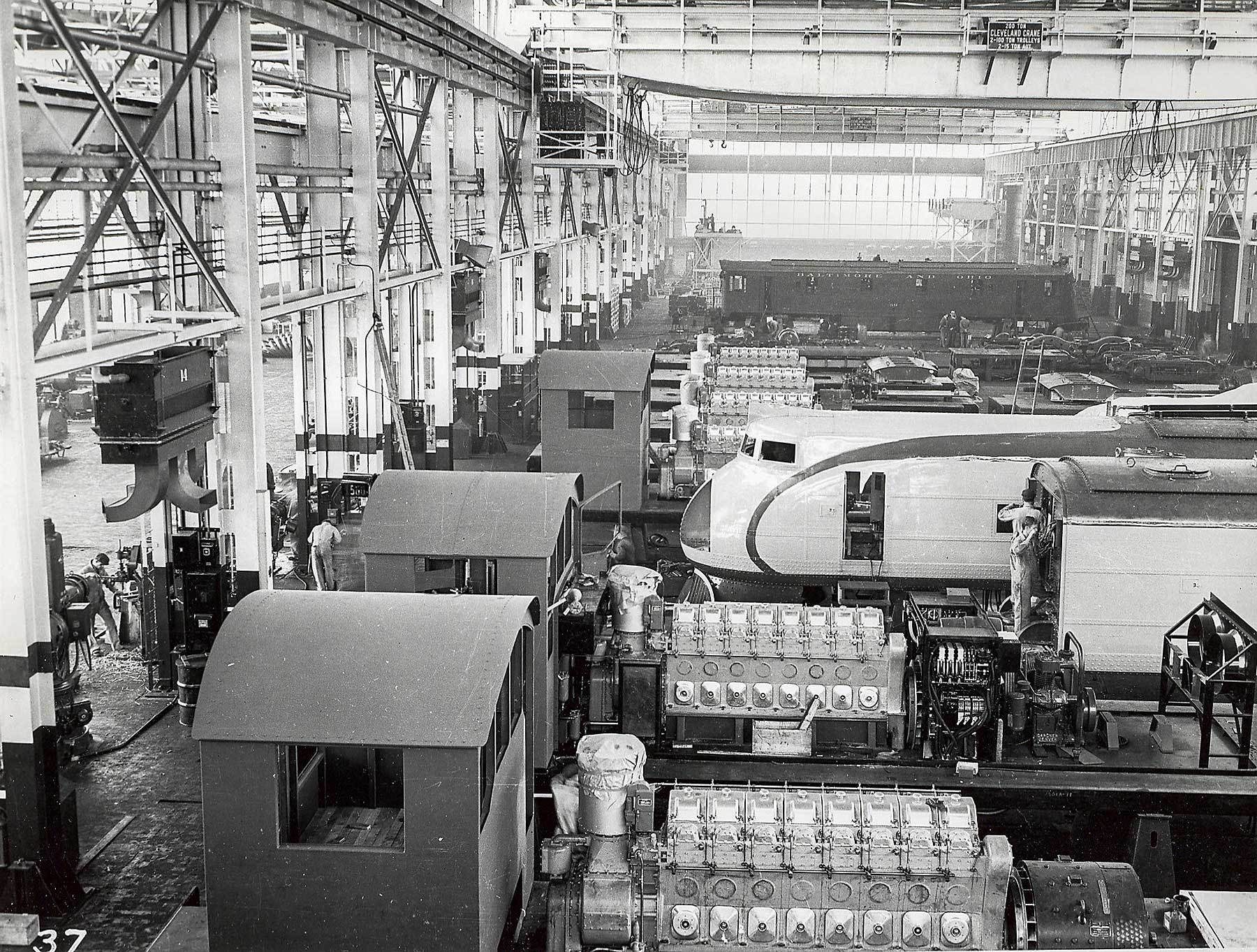
The evolution from steam to diesel did not occur overnight. It actually played out over several decades. But, EMD was instrumental in sparking the change. Ironically, the transition had many similarities to what’s happening today in the automotive industry with the switch from internal combustion engines to battery-powered vehicles.
Engineers at EMD played a lead role in spawning the diesel era in America and elsewhere. Legacy steam locomotive builders such as Alco, Baldwin and Lima, which dominated the market for decades, were slow to adopt and soon found themselves playing catch up.
However, by then it was too late. By being first to market, EMD carved out a competitive advantage that was virtually a monopoly, before GE eventually caught up in the 1980s.
The 1940s and 1950s was an unprecedented transition period for the U.S. railroad industry as steam power slowly succumbed to diesel technology, which offered numerous advantages.
Steam locomotives were a proven, but labor-intensive technology. They required a complex network of strategically located coaling stations, water tanks, back shops and roundhouses.
Diesels were easier to operate and required only one operator, which provided greater ease in switching and yard operations. They were quieter, operated in all types of weather and provided climate-controlled cabs for an improved work environment. Diesels also offered instantaneous start-up and stopping ability, and they incurred no costs due to downtime.
In 1939, this FT freight locomotive embarked on an epic 11-month journey around the United States that convinced many railroads to switch from steam to diesel power. Photo by Austin Weber
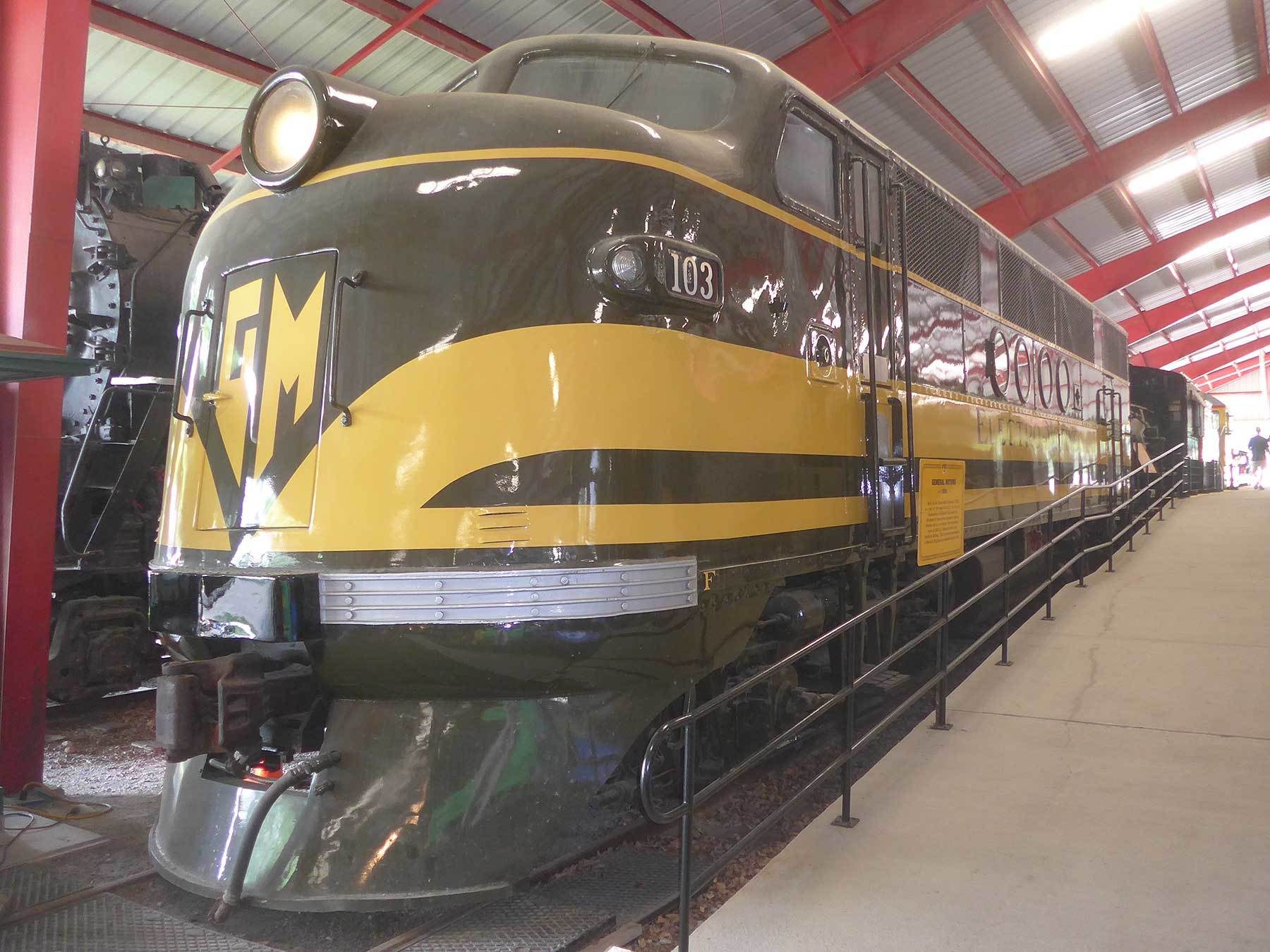
“[Diesel-electric locomotives were] an ‘automatic’ machine that did not require constant human attention like a steam locomotive, which would run itself out of fuel and water if not properly manned,” says Jim Boyd, author of The American Freight Train. “And the diesel could run all day on a tank of fuel and not need to visit the roundhouse or ashpit every few hours to have its fire cleaned or machinery lubricated.
“Whereas even a modern steam locomotive generally could not run more than about 250 miles before being pulled off the train and serviced, a diesel set could run a thousand miles or more and then continue on with nothing more than a quick refueling,” notes Boyd.
In addition, many steam locomotives were custom-built products, often costing as much as 25 percent more than their diesel equivalents that could be more easily mass-produced. Diesels quickly grew in popularity due to uniformity of construction and less complex, readily available parts.
EMD engineers relied on GM’s managerial expertise, supply chain efficiency and production prowess to dominate the industry. By 1953, GM held a whopping 73 percent of the U.S. locomotive market, followed by Alco at 15 percent.
By the mid-1960s, GE had bumped Alco from its No. 2 spot. But, in 1968, GE only accounted for 22 percent of the market vs. 70 percent for EMD. Between 1968 and 1980, average annual production for EMD was 992 units vs. 281 for GE.
This overhead shot from the mid-1950s shows the engine assembly line. Each massive engine rode on a flanged wheel carriage that was moved down the line by winch or forklift. Photo courtesy Progress Rail Services Inc.
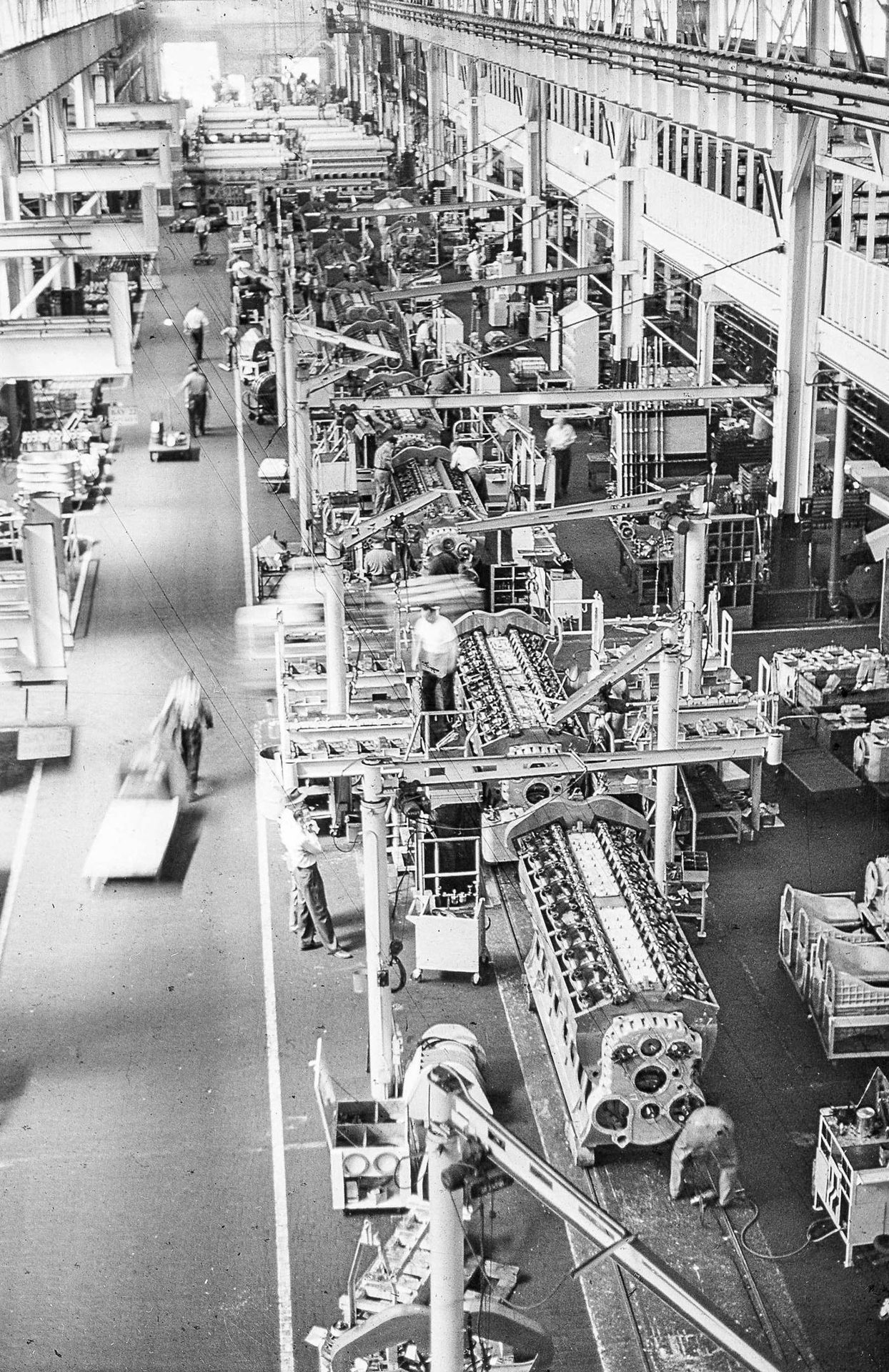
Innovative Products
This ground level view shows a fresh batch of diesel engines being tested in the 1980s. Engines were mounted on a large, tracked dolly that allowed them to be moved in and out of the test cell. Photo courtesy Preston Cook
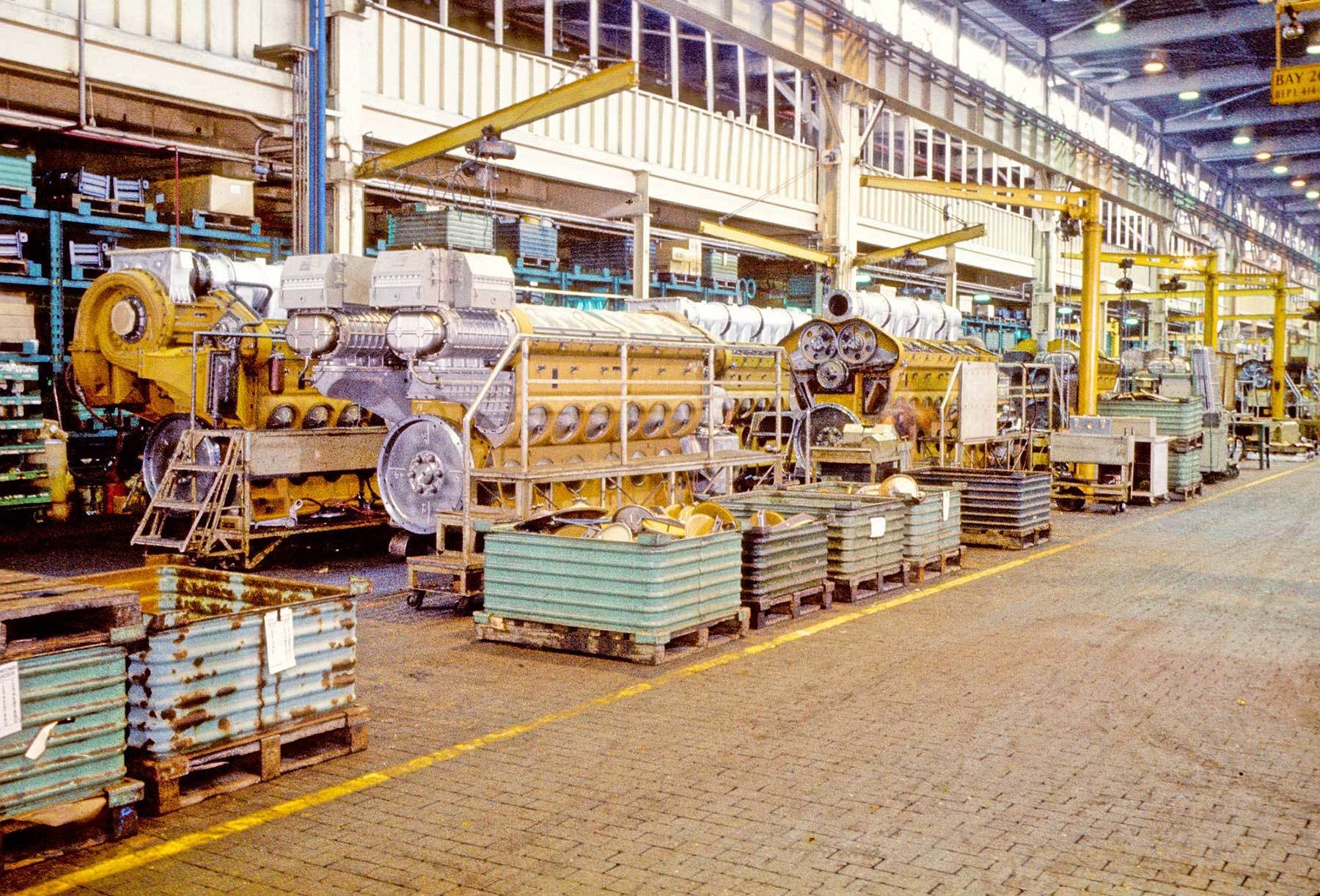
Unlike steam locomotives, which were custom-designed and built to meet the specific operating needs of individual railroads, EMD offered off-the-shelf machines that could do the same job better and cheaper. The company offered a few standard but versatile models that were backed up with technical support, training and readily available parts.
However, diesel-electric locomotives required a new type of mindset for design engineers and manufacturing engineers. Instead of dealing with a mind-boggling array of water pipes and steam tubes that were used in steam locomotives, they had to focus instead on high-voltage cables and electrical controls. Boilers, fireboxes, injector valves and pistons were replaced with control cabinets, generators, traction motors and wiring harnesses.
The basic layout of locomotives also changed, except for humble yard switchers. One of the most dramatic differences between steam and diesel-electric power was the cab where drivers sat. New designs, such as EMD’s revolutionary E-unit, placed locomotive crews at the front end of trains for the first time.
These bulldog-nosed locomotives were a common sight on America’s railroads during the 1950s and 1960s. Photo courtesy Progress Rail Services Inc.
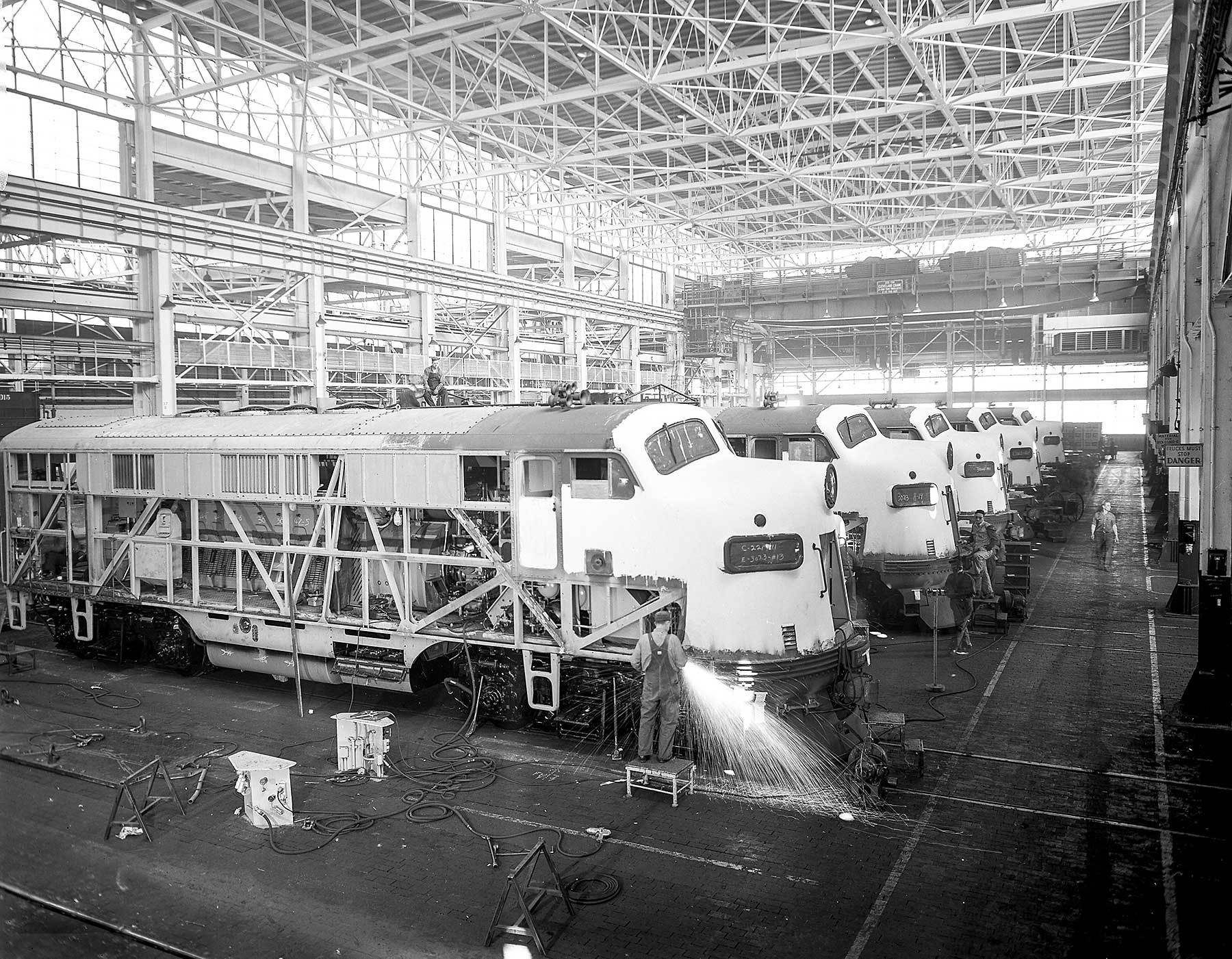
“The locomotive crews of heavyweight passenger trains, accustomed to riding behind the ‘protection’ of a 200-ton, 70-foot boiler were wary of their vulnerable position at the front of [early diesels], where they would be the first to arrive on the scene of any mishap,” says Boyd. “So Electro-Motive went to work to move the engineer away from the front window. This resulted in an overall larger locomotive in what became known as the ‘covered wagon’ car body with the engineer’s control cab at one end.
“Realizing the market potential for this new locomotive, General Motors put its automotive design talents to work on styling this new streamliner,” explains Boyd. “The result was an absolute classic of Art Deco design, with an elegantly slanted nose and smoothly contoured front cab windows. This was not only a fast and powerful locomotive; it looked like a fast and powerful locomotive!
“Knowing that it would take two or three of its new diesel-electrics to equal or surpass the performance of a steam locomotive, EMD adopted the concept of optional cab and booster units,” adds Boyd. “The cab units, known as ‘A-units,’ had the engineer’s control cab at one end, while the booster ‘B-units’ had no cab whatsoever and would simply be inexpensive ‘building blocks’ to increase the horsepower behind the cab unit.”
Diesel Power
During World War II, EMD mass-produced diesel engines for U.S. Navy ships. Photo courtesy General Motors
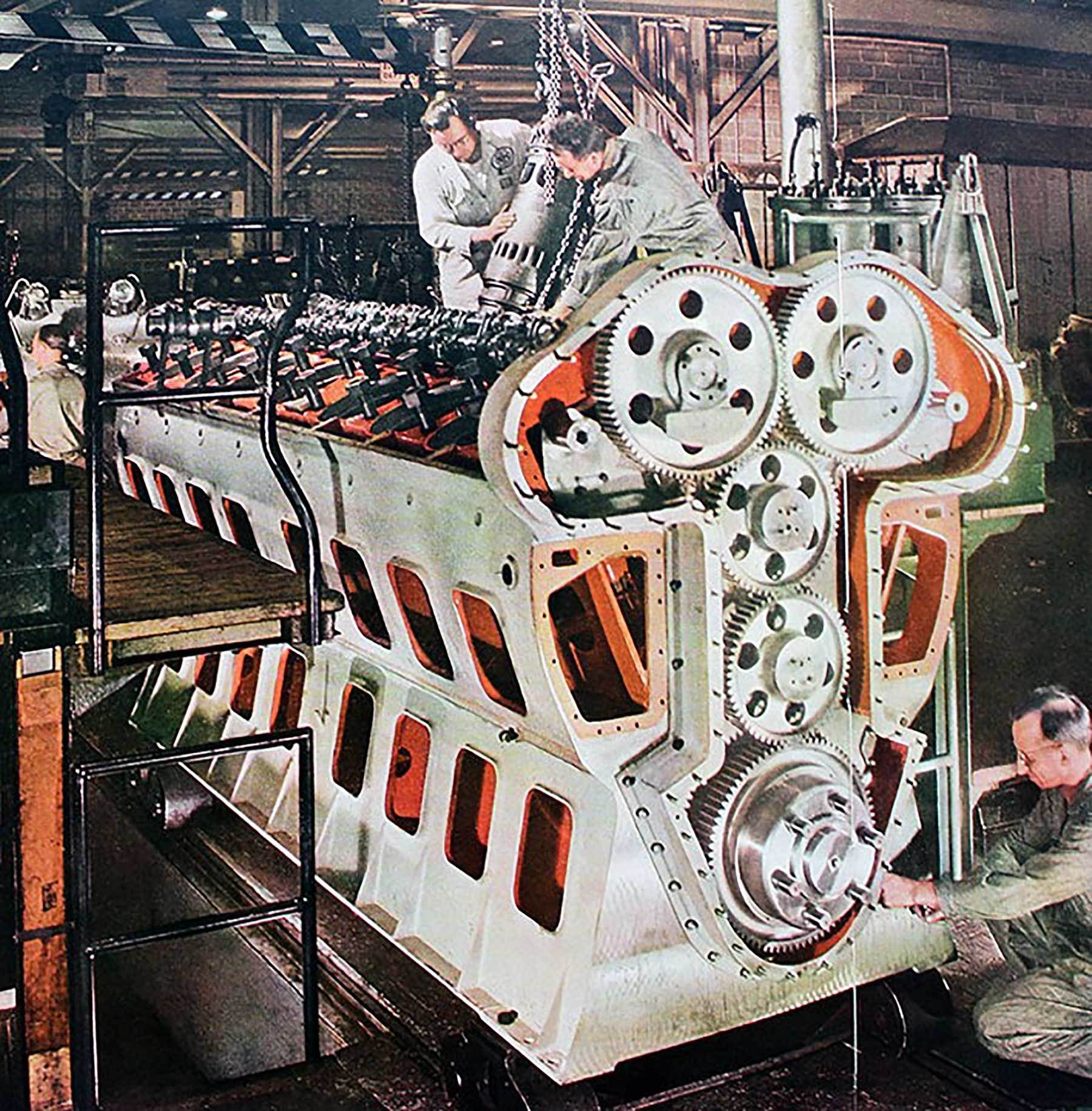
To power their machines, GM engineers developed a prime mover that featured a high degree of standardization and interchangeable parts. The 567-model diesel engine was designed for easy maintenance. Connecting rods, cylinder heads and liners, injectors, pistons and other parts could be easily removed.
The Model 567 came in three sizes, including a 600-hp V-6, a 1,000-hp V-12 and a 1,350-hp V-16. It eventually went on to power more than 25,000 locomotives produced by EMD over the next 28 years
The Santa Fe Super Chief was the first full-sized passenger train designed from the onset to use diesel-electric power. The popular streamliner and its long, slanted nose E-unit debuted in 1937, hauling people between Chicago and Los Angeles. Other early adopters of EMD products were the Baltimore & Ohio, Burlington, Chicago & Northwestern and Rock Island railroads.
“While passenger trains got the glamour and glory, [General Motors] knew that the really big market was the 50,000 steam freight locomotives that were is service at the time,” says Boyd.
To address this lucrative niche, EMD engineers unveiled a groundbreaking design in 1939 dubbed the FT. It featured a V-16 diesel engine, four generators and 16 traction motors.
To promote the new machine, EMD sent the locomotive on an 11-month journey around the United States, visiting various railroads. The nearly flawless tour of 35 states covered more than 80,000 miles and proved to be an enormous success. Most of the railroads that tried “the diesel that did it” placed orders.
EMD built more than 2,500 GP7 locomotives between 1949 and 1954 for general-purpose applications on American railroads. Photo courtesy Illinois Railway Museum
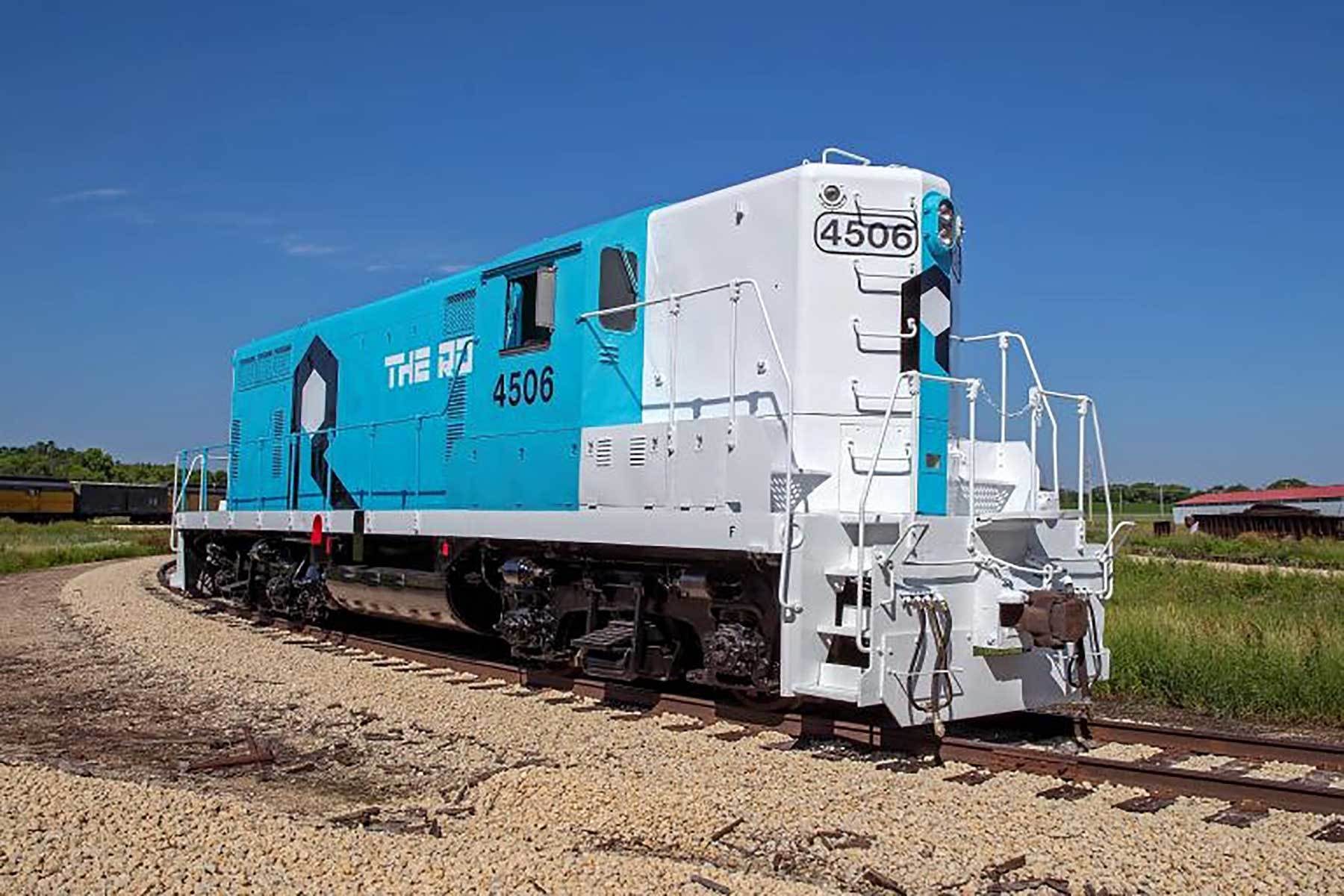
“The introduction of the FT changed how railroads viewed motive power,” says Brian Solomon, author of Streamliners: Locomotives and Trains in the Age of Speed and Style. “This model showed for the first time that a diesel could match and exceed the output of big steam.
“The FT was designed to operate almost anywhere, giving diesels greater availability, better thermal efficiency, better economy and overall lower cost of operation,” explains Solomon. “GM’s FT was an outgrowth of the successful passenger E-unit design, and the essential technology refined for the E-unit had been adapted and rearranged for the FT. In addition to similar mechanical and electrical systems, the two types shared the same essential streamlined car body.”
The “bulldog” nose, which featured a distinctive 80-degree slant that was introduced with the FT, was a design refinement over the steeply slanted front of early E-units.
“This nose was more than just good looks,” Solomon points out. “It was a heavily reinforced buffer designed to protect crews in the event of a collision, while giving them a superior forward view.
This photo from the late 1950s shows a few of the traction motors and other electromechanical components needed to assemble a diesel-electric locomotive. Photo courtesy General Motors
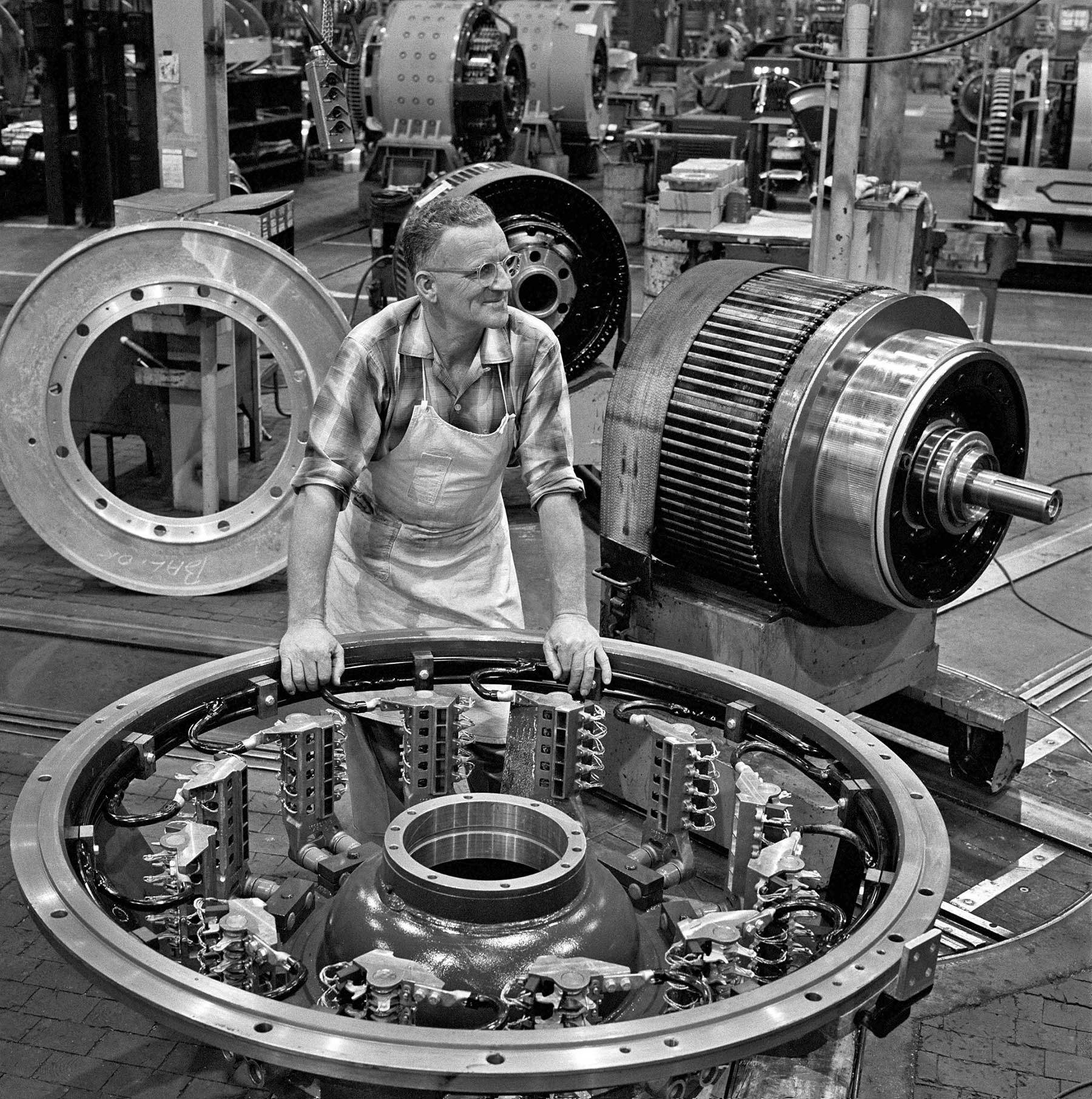
“The nose section was constructed from four separate sheets of pressed 12-gauge steel combined with a cylindrical headlight housing welded to the locomotive car body frame,” says Solomon. “Reinforced underframing provided additional structural support.
“The compound curves connecting sheet steel and headlight housing were made from automotive bonding putty,” adds Solomon. “The style, slope and angle of windshields were similar those featured on late-1930s Buick automobiles. Inside the cab, the handles used to roll down the windows were virtually identical to those in GM automobiles.”
Over a 21-year production run that ended in 1960, more than 7,600 F-units were sold in North America. The groundbreaking machine was soon followed by several other breakthroughs that revolutionized railroads and ended the steam era.
In 1940, North American railroads only had 797 diesel locomotives in service vs. 40,041 steam locomotives. A decade later, 14,047 diesels were in operation vs. 25,640 steam locomotives. EMD produced its 10,000th unit in 1951 and its 25,000th locomotive in 1962.
The company’s frenzied rate of production was only interrupted by World War II, when it mass-produced diesel engines for U.S. Navy ships, such as landing craft and submarine chasers.
Locomotive assembly quickly ramped up again in 1946. By that late 1940s, EMD was the undisputed market leader, and the McCook, IL, factory was known as the locomotive capital of the world. In 1949, the company launched several new products that cemented its reputation, such as the GP7 locomotive for general-purpose applications.
Fabulous Factory
EMD’s factory in McCook, IL, was a vertically integrated facility that produced many components in-house. Photo courtesy Preston Cook
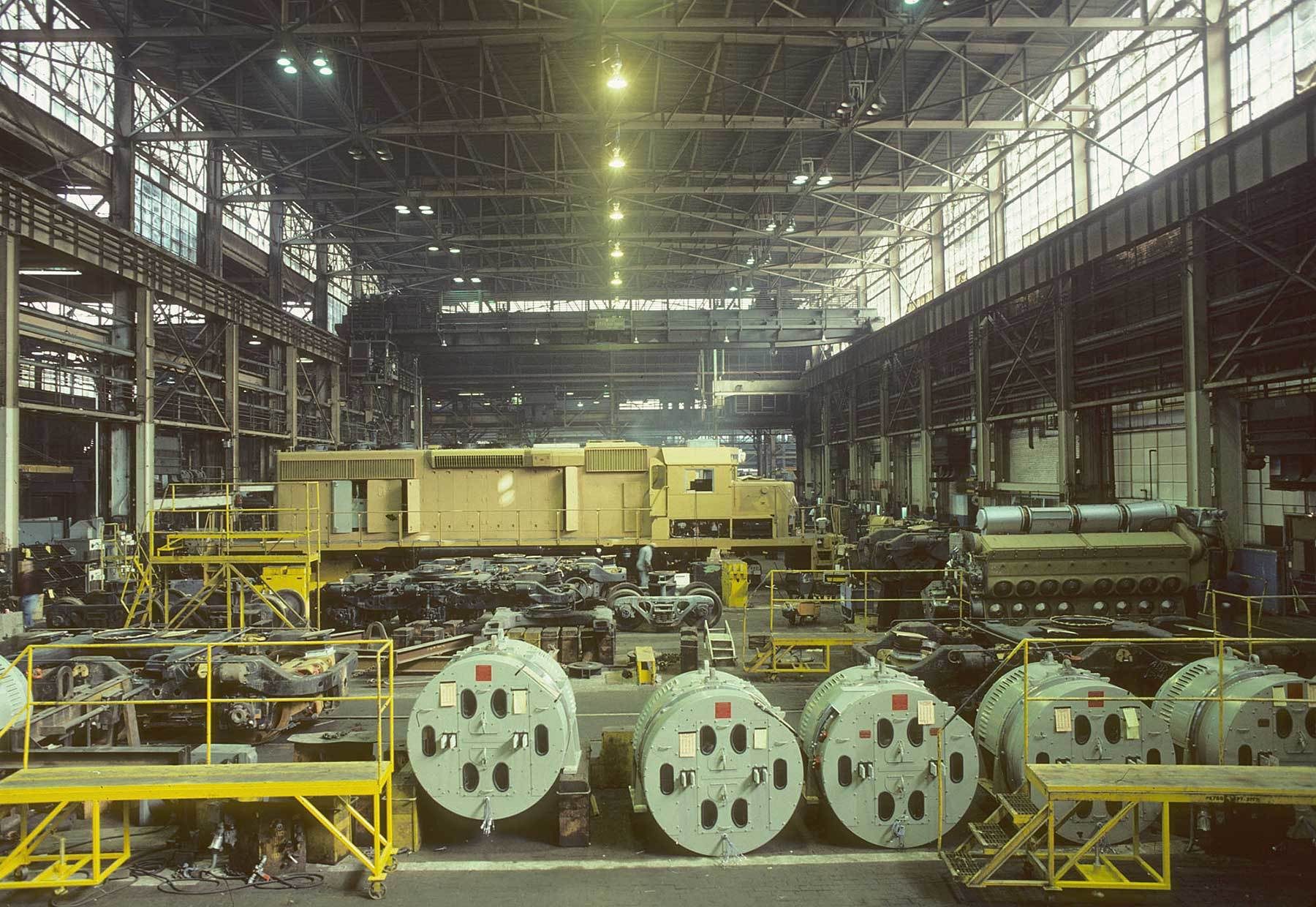
For decades, the heart and soul of EMD was its factory in McCook, which was often identified as “LaGrange,” because it used that nearby town as a mailing address. During its heyday, the huge complex featured 4-million-square-feet of production space and employed as many as 14,000 people.
It was one of the largest industrial facilities in the Chicagoland area, which at the time boasted several other impressive facilities, such as the famous Calumet Shops of Pullman-Standard Co. Other local manufacturing landmarks included the Great Works of Crane Co., the Harvester Works and Tractor Works of International Harvester Co., the South Works of U.S Steel and the Hawthorne Works of Western Electric Co.
EMD’s factory was a vertically integrated facility that machined, pressed, stamped and welded its own parts and fabricated bodies, cabs, chassis and fuel tanks. The company produced its own AC and DC alternators, generators, traction motors, wiring harnesses and other electromechanical components, such as armatures, bus bars, electrical cabinets, housings, pinions, rotors and stators.
This 1969 aerial view looking northwest shows the heart and soul of EMD. The facility mass-produced more than 50 percent of all diesel locomotives in use in the United States. Photo courtesy Progress Rail Services Inc.
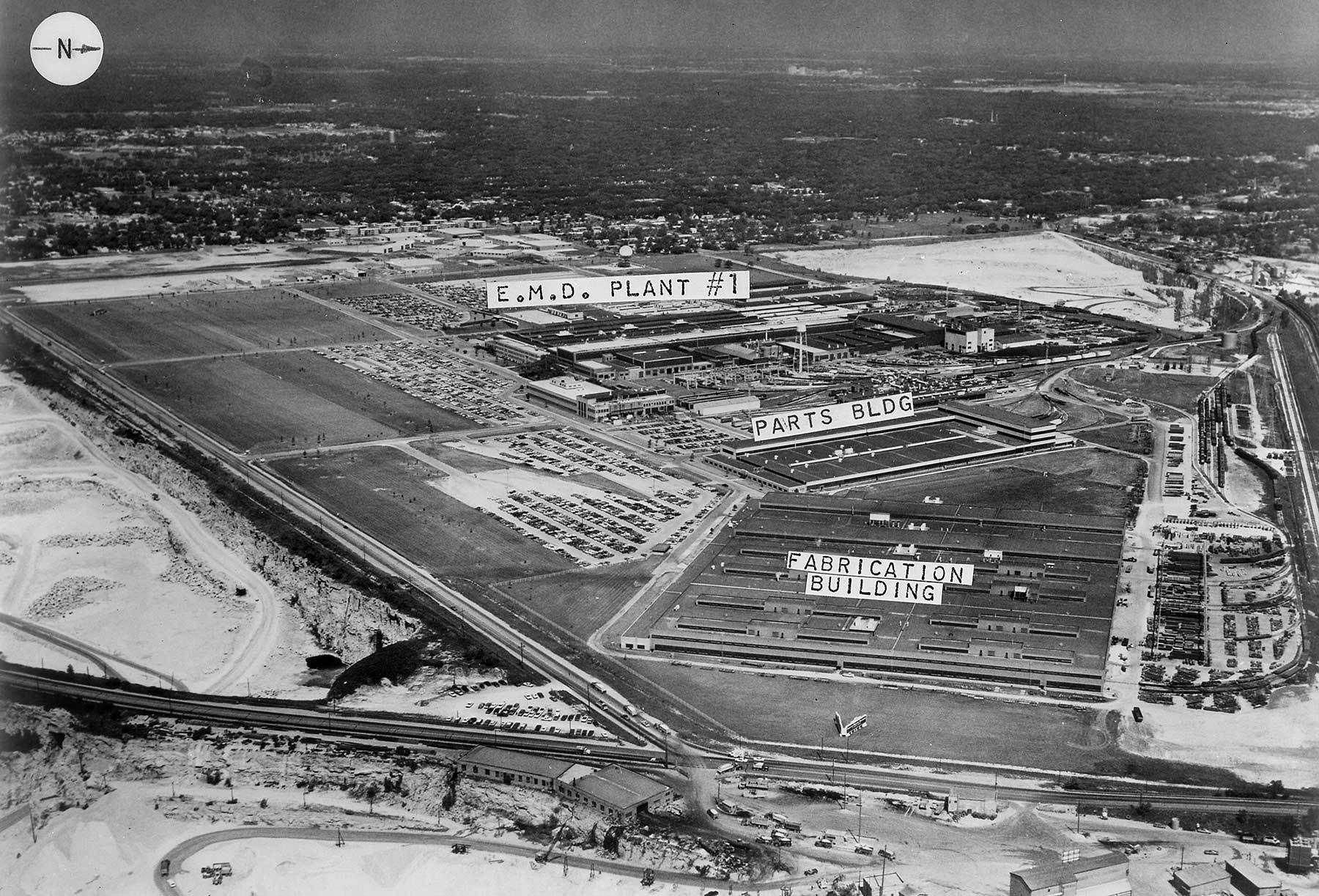
However, EMD also acquired some items from Delco, Ternstedt and other GM subsidiaries. A few parts, such as air brakes, bells and lights, crankshafts, meters, seats, truck frames, wheels and windows, were purchased from third-party suppliers.
The heyday of EMD was from approximately 1940 to 1980. During that time period, the factory was a beehive of activity, turning out an average of five locomotives a day. In addition to machines produced for use in North America, EMD exported hundreds of products to Africa, Australia, Europe, the Middle East and South America.
At peak production, the facility could build 11 diesel engines a day. In addition to powering electric generators in locomotives, the engines were produced for various types of marine and stationary power applications.
Complex Assembly
EMD used a series of colorful advertisements to promote its products, such as this example from the mid-1940s that says “smart travelers say the best trains follow General Motors locomotives.” Illustration courtesy Preston Cook
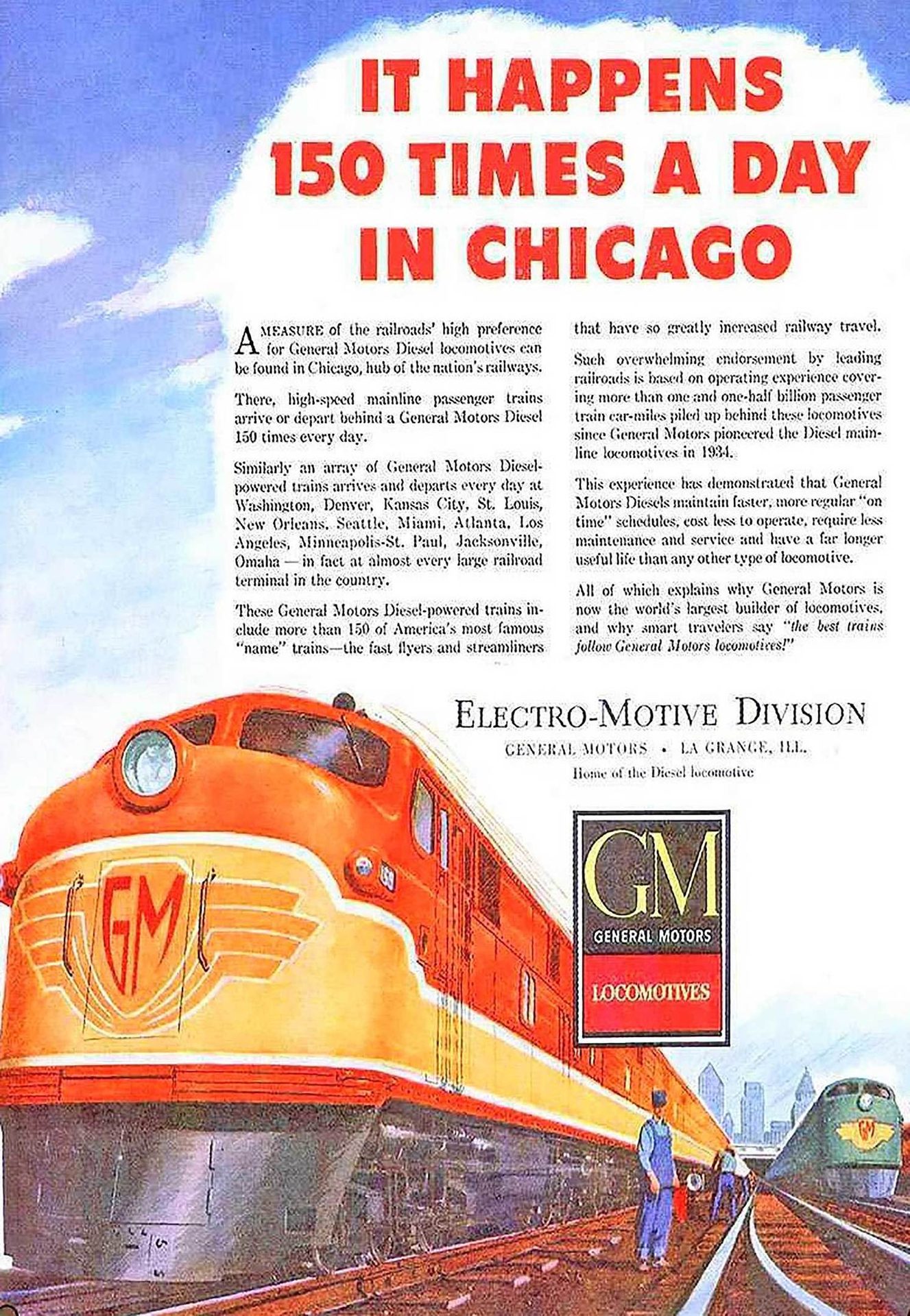
The McCook complex was comprised of two main buildings, which were referred to as Fabrication and Plant 1. The latter facility, constructed in the 1930s and 1940s, housed the engine, transmission and locomotive divisions that assembled diesel engines, generators, traction motors and other subassemblies. It also was home to a large, high-bay locomotive erecting hall, where final assembly took place. A series of expansions eventually enlarged Plant 1 to four times its original size.
Large components and entire locomotives were moved around the plant via heavy-duty overhead cranes. “Locomotives in various stages of assembly were leapfrogged from one workstation to another with a 200-ton crane,” says Preston Cook, a retired mechanical engineer who worked for EMD in the 1970s and 1980s. “Production flowed from south to north, but final assembly occurred in the middle of the facility.
“When the plant was operating near peak capacity of around five units a day, the space in the high bay was in great demand,” adds Cook. “It was extremely critical that partially completed locomotives be moved among the various assembly areas as quickly and efficiently as possible.”
Small hoists were positioned throughout the factory. However, despite being owned by a large automaker, EMD did not use any conveyors. In fact, the only thing that came close to a moving assembly line was located in the engine department.
“Diesel engines were mounted on large carriages or skids equipped with flanged wheels,” explains Preston, who was in charge of plant tours and produced an extensive educational program for local school groups and other organizations. “There were two parallel tracks laid in the floor of the assembly line. Dollies were pulled by a winch or pushed along by forklifts toward the north end of the line, where the test cells were located.”
Because of a series of hastily planned additions needed to accommodate unprecedented growth, production flow and layout was not ideal in many parts of the facility. Ironically, the original building was designed by legendary architect Albert Kahn, who was the mastermind behind many famous factories in the auto industry, including Ford’s Highland Park plant and GM’s Willow Run facility.
“It was a very inefficient plant layout,” recalls Cook. “There was lots of forklift traffic and the flow of material didn’t always make too much sense. You had to be very alert and quick on your feet to move out of the way.
Large components and subassemblies were fabricated at EMD’s Pullman plant on the South Side of Chicago. These assembly lines are producing two different types of locomotive cabs. Photo courtesy Progress Rail Services Inc.
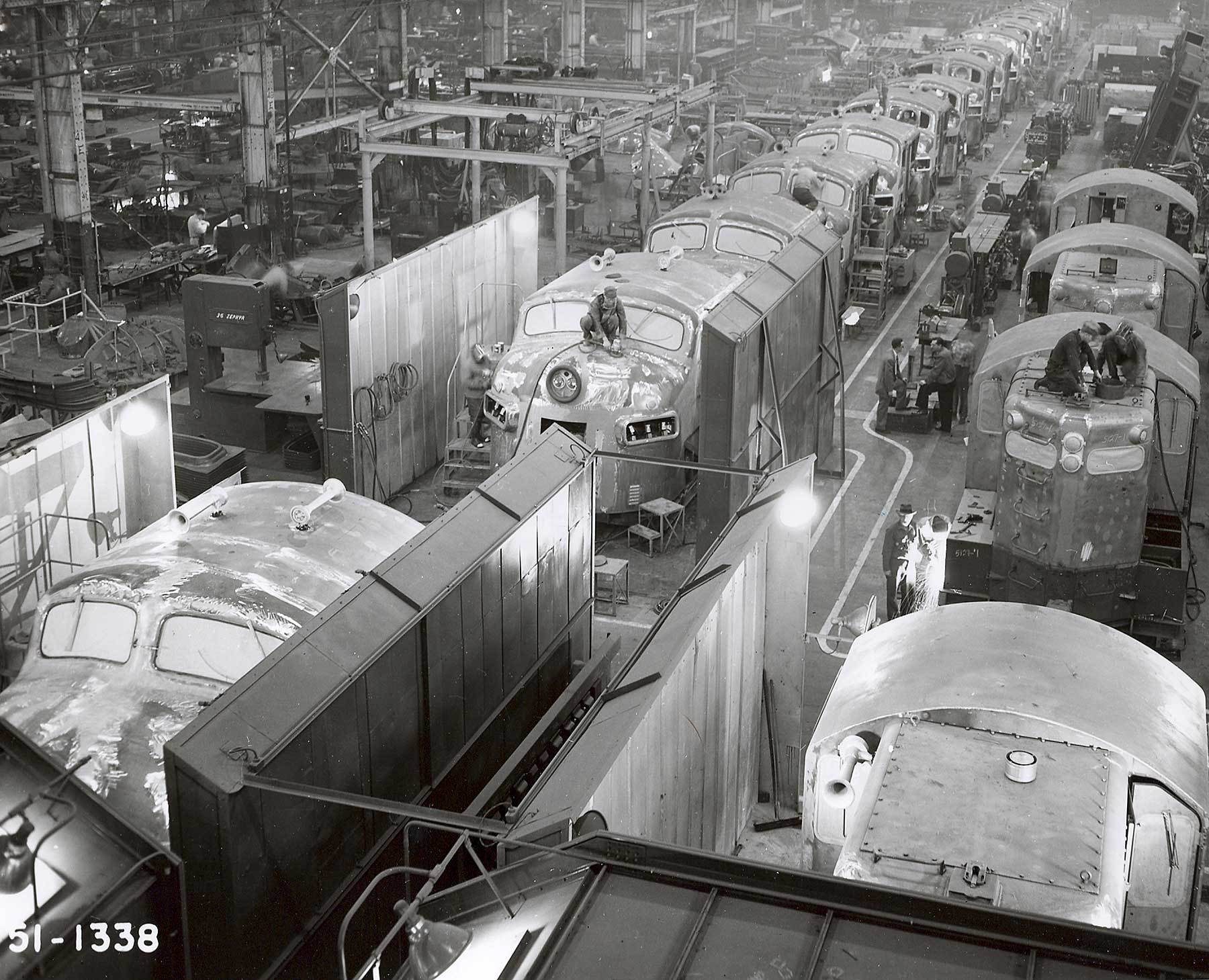
“Processes were grouped together, but often not the most efficiently,” claims Cook. “Machinery was not always located in the logical sequence that it needed to be in. Many large tools, like boring and milling machines, were fixed in place. Some legacy machine tools, such as drill presses and tube benders installed during World War II, were still in use in the 1970s.”
In the days before OSHA, it was a very noisy and chaotic environment. The constant clatter of air tools and riveting guns filled the air, while hoses and ladders posed constant trip and fall hazards. Lots of hand tools were also used throughout the factory, and occasionally dropped by assemblers working above.
For many years, EMD was one of the largest consumers of welding rods in the United States. In some parts of the plant, the air was thick and hazy from welding fumes. According to Preston, during the summer months, smoke from welding operations tended to mix with the moisture in the air, which caused fog to form in some parts of the factory.
This view shows part of the cab assembly line in the 1980s. Photo courtesy Preston Cook
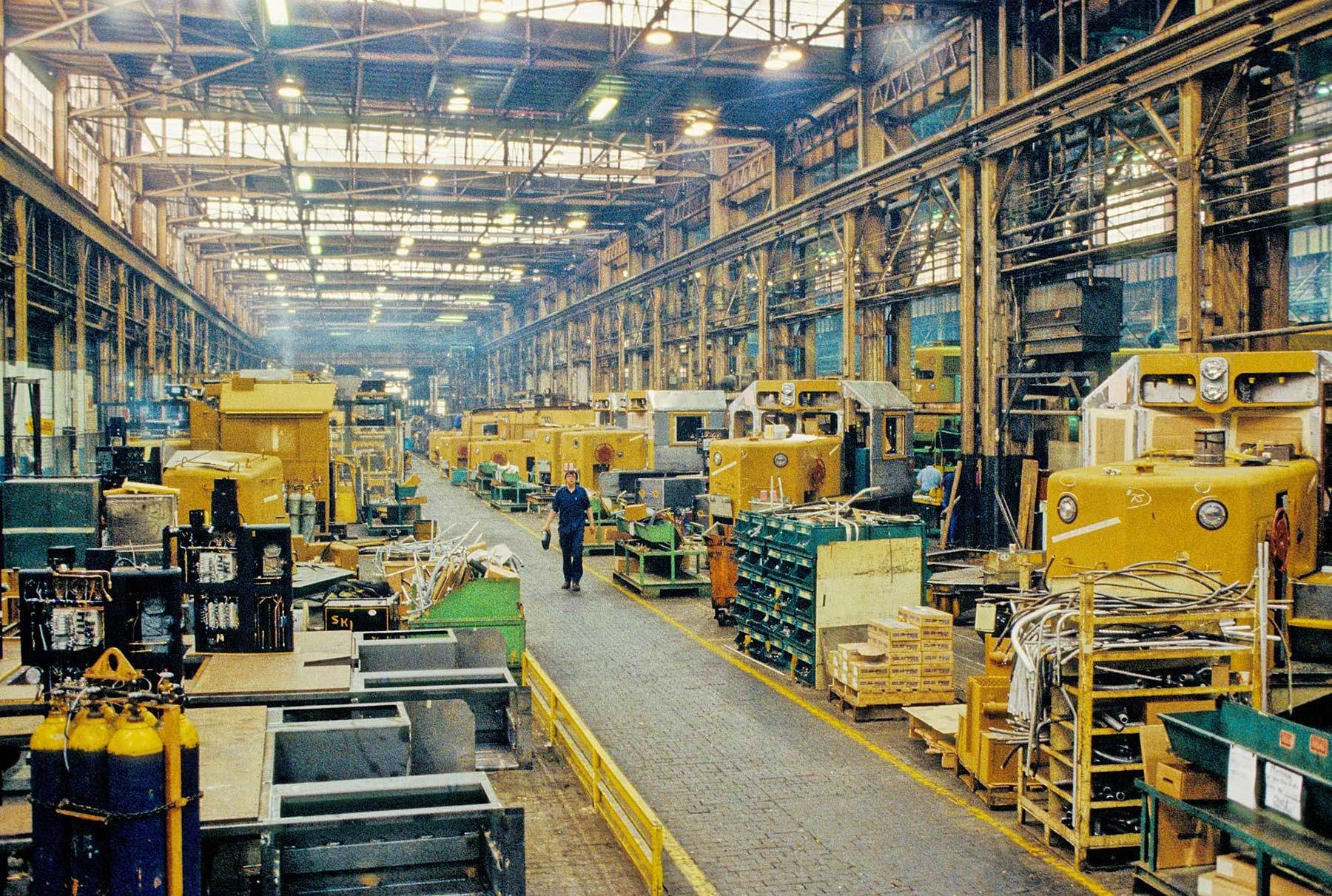
In 1954, EMD opened a fabrication building near Plant 1 that specialized in bending, cutting and welding heavy steel subassemblies. It produced hoods, underframes and other bulky objects that were shipped to Plant 1 via railroad flatcars.
Other parts of the McCook complex housed offices and inspection facilities, including a test track. A styling department and paint shop turned out colorful, visually unique designs and graphics that changed the face of railroading. Instead of dull, black steam locomotives, many EMD diesels sported colors that evoked glamour and speed to a Depression- and war-weary public, such as Illinois Central’s “City of Miami,” Rock Island’s “Rocket” and Santa Fe’s famous “warbonnet” paint schemes.
Boom and Bust
The E-unit locomotives helped end the era of steam-powered passenger trains. Photo by Austin Weber
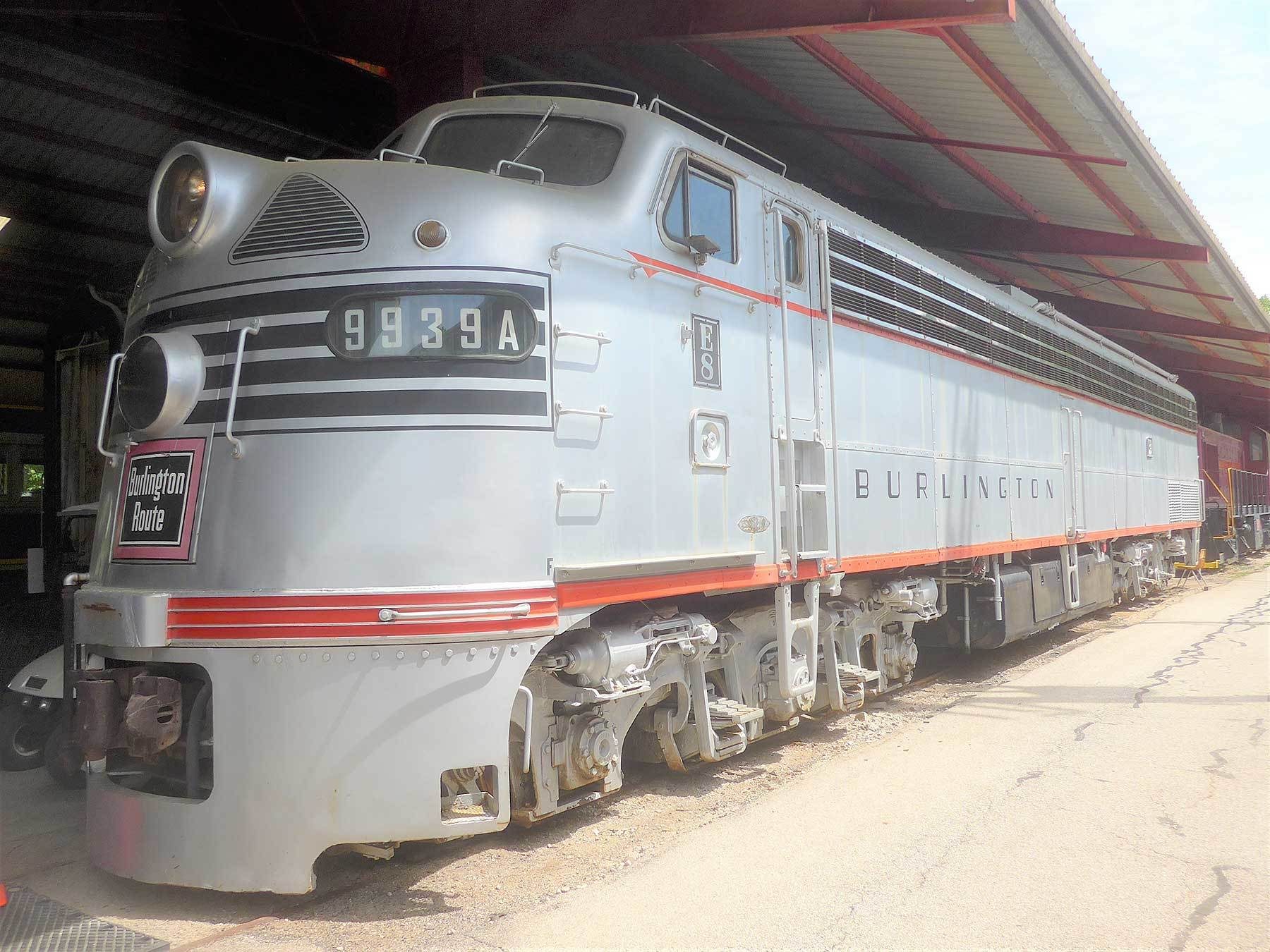
In addition to the main complex in McCook, EMD operated several other factories during the boom years. In 1946, it acquired a Pullman plant on the South Side of Chicago that produced aircraft parts during World War II. The 700,000-square-foot facility, known as Plant 2, operated until 1982. It specialized in producing air boxes, cabs, crankcases, fuel tanks, hatches, oil pans, traction motor frames and other subassemblies that were trucked to Plant 1.
From 1948 to 1954, EMD operated a factory in Cleveland that mass-produced switchers. After assembling 3,613 units, the facility was transferred over to GM’s Euclid division for assembly of earthmoving equipment.
This view from the early 1960s shows a GP30 freight locomotive being carefully lowered onto its trucks by a large overhead crane. Photo courtesy Progress Rail Services Inc.

In 1948, GM also opened a plant in London, ON, to produce locomotives for the Canadian market, which was beginning to shift away from steam.
From 1981 to 1990, production at EMD fell by two-thirds, from 843 locomotives a year to only 255. In 1988, the company announced that it was shifting all locomotive production to the much smaller General Motors Diesel Ltd. factory in Canada, because manufacturing costs were cheaper there at the time.
Plant 1 produced its last locomotive in 1992—an F40 unit for Chicago’s Metra commuter railroad. During a 56-year span, the factory turned out 14,750 machines.
This wiring harness is being assembled with Faston connectors. It was later installed in the main electrical cabinet of a locomotive. Photo courtesy Preston Cook
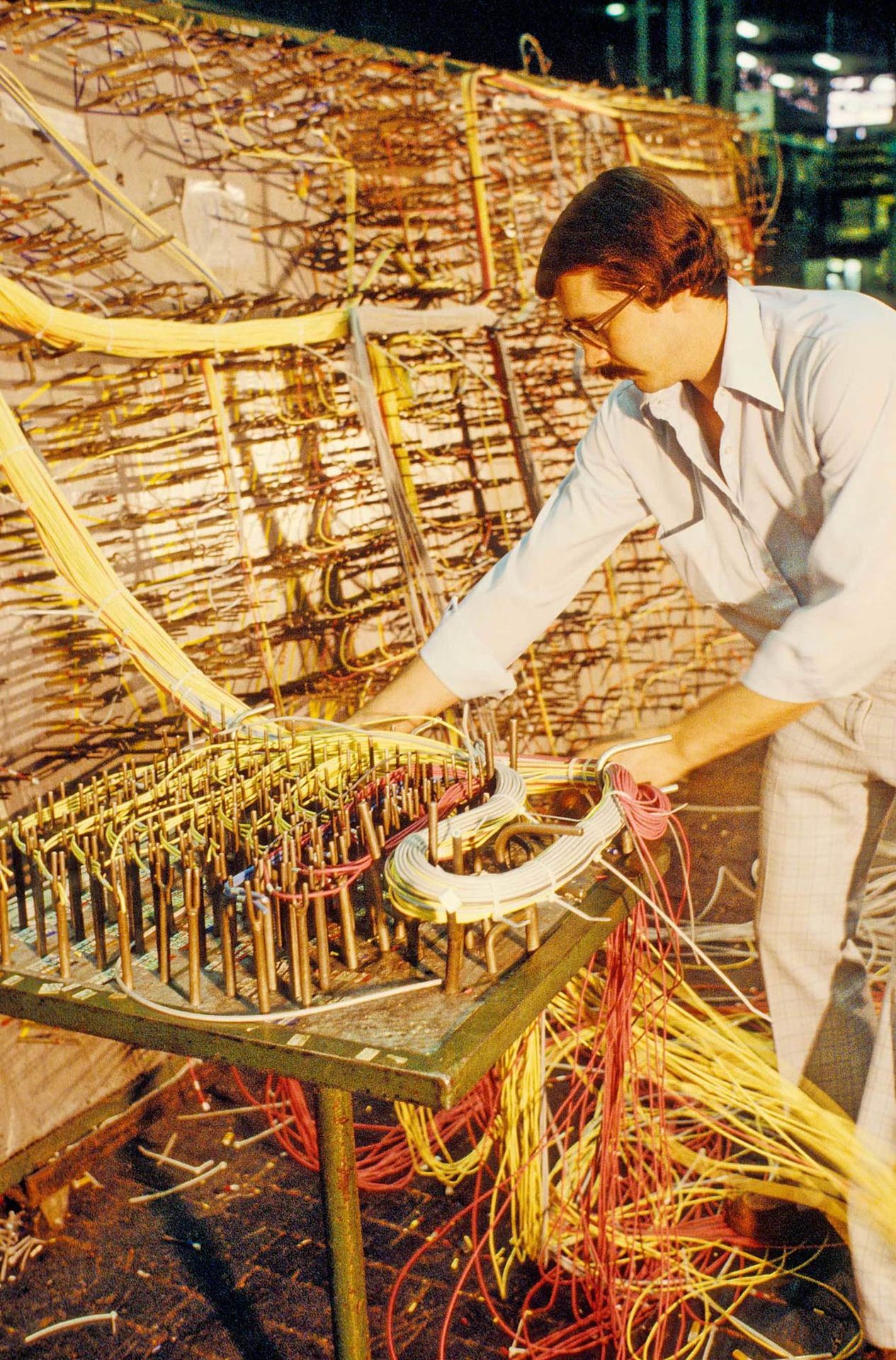
By the early 1990s, EMD had lost its way. The company was dethroned by General Electric in the 1980s. And ever since, GE Transportation (now Wabtec Corp.) has aggressively defended its No. 1 position by investing in production facilities and applying a variety of lean manufacturing and quality control initiatives.
Diesel engine assembly continued at the McCook facility until 2018, when Caterpillar moved production to a newer facility in Winston Salem, NC. However, several unused buildings at the once-bustling complex, including the legendary Plant 1, were demolished in 2000 as part of a downsizing effort.
Today, EMD’s former 383-acre site in McCook is partially vacant and some of the land is now occupied by warehouses. But, a few of the most famous products assembled at the facility are preserved and on display at places such as the Baltimore & Ohio Railroad Museum in Baltimore; the Illinois Railway Museum in Union, IL; and the National Museum of Transportation in St. Louis.
EMD’s legacy also lives on at Progress Rail Services, which operates a state-of-the-art assembly plant in Muncie, IN, that opened in 2011 at the site of a former ABB factory. The company produces a variety of locomotives for freight and passenger applications, including sustainable products that feature zero exhaust emissions. It is currently building a fleet of battery-powered Joule machines that will be used by Union Pacific and other railroads in the near future.
The streamlined locomotive in the foreground is being assembled for the Union Pacific’s “City of San Francisco” passenger train in 1936. Various switchers are in production behind it. Photo courtesy Progress Rail Services Inc.
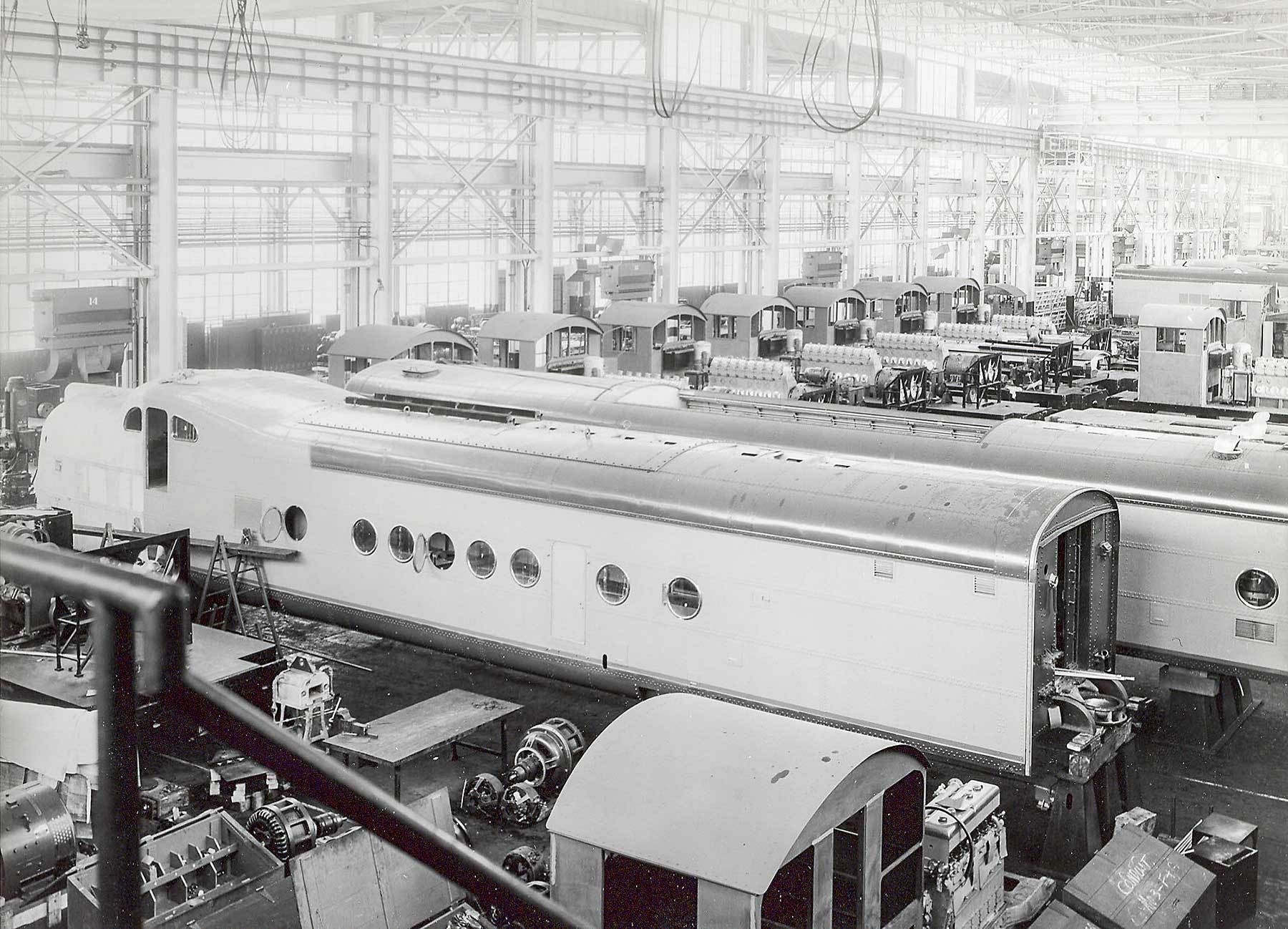
ASSEMBLY ONLINE
For more information on locomotive manufacturing, visit www.assemblymag.com to read these articles: