ASSEMBLY ESSENTIALS
Assembly Solutions in E-Mobility
Regarding technical cleanliness, DEPRAG has developed its complete CleanFeed concept with specific CleanFeed components; this includes elements for low-abrasion part feeding to minimize the accumulation of damaging particles from the outset. Sword feeders, for example, are incredibly gentle at sorting, separating, and supplying fasteners. Sensors on the device automatically determine the number of strokes necessary so that stroke movement, and therefore abrasion, are kept to a minimum.
Furthermore, hoppers help keep a consistently low quantity of fasteners in the feeding system, because fewer screws mean less contamination. Since the generation of particles cannot entirely be eliminated, suction systems also serve as an effective method of creating cleanroom conditions. The DEPRAG “Particle Killer” targets and removes particulates before assembly and ejects them through a filter. On the other hand, an SFM-V vacuum screwdriving module uses suction to remove residual dirt directly from the screwdriving tool via additional vacuum sources. As well as modifications to the hardware, particle contamination can also be addressed through intelligent adjustments managed by the controller, such as a reduction in speed during bit engagement with the screw head; this has the added benefit of reducing wear and tear on the tool.
Finally, because productivity plays an essential role in the mobility sector, DEPRAG has developed a new digital service, the “Cockpit,” facilitating an easy introduction to the interconnected factory. This software allows for the supervision and analysis of assembly tasks and provides analysis tools for continuous process optimization and the recognition of trends. The data from a company’s various factory locations, its production lines, and connected devices are collected centrally by the system. Data can even be collected from production locations spread throughout the world.
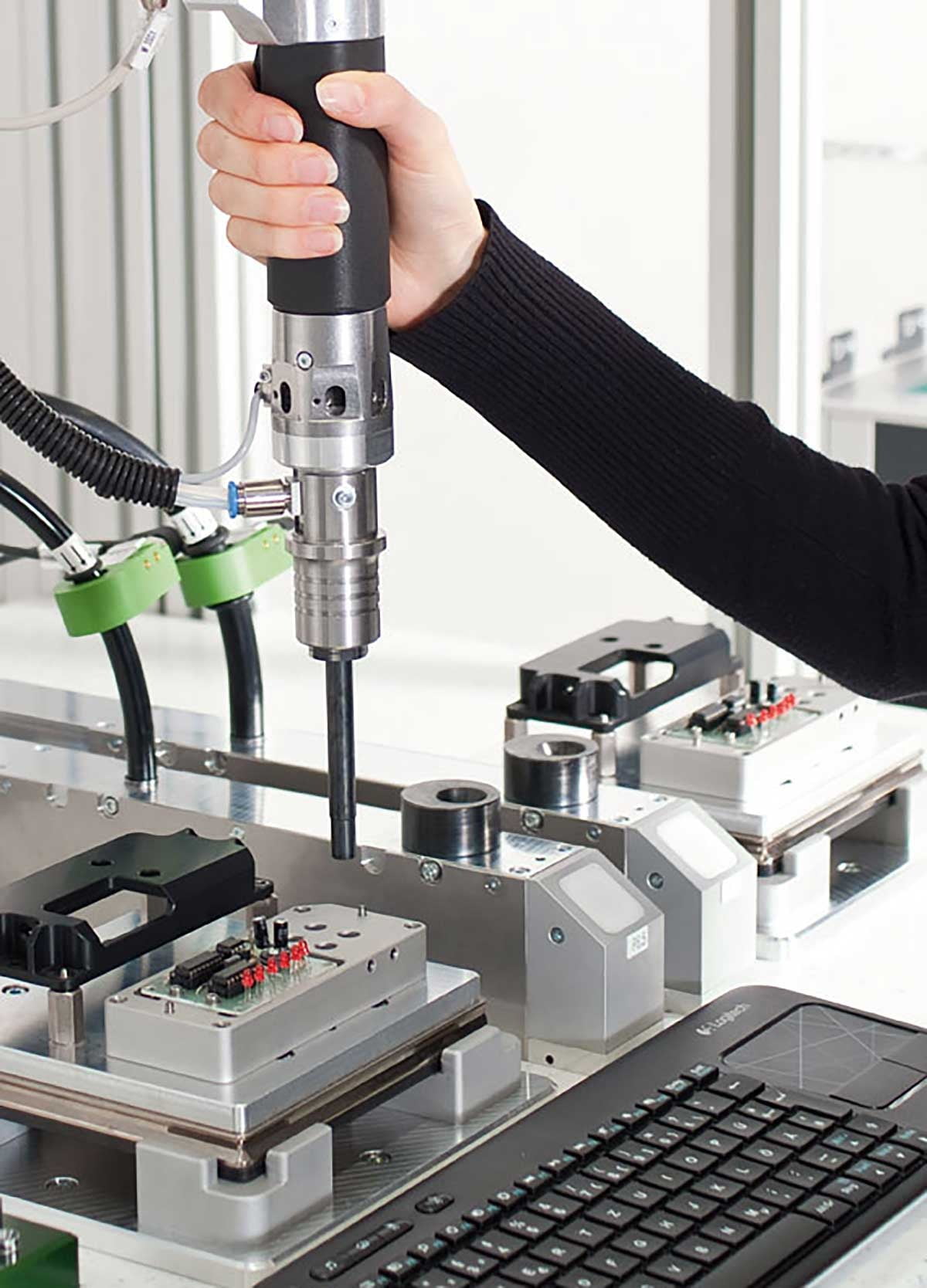
Electromobility is the definitive key technology for the sustainable transport system of the future. The policy-assisted development of E-mobility is moving in the right direction. However, the automotive industry and its suppliers still find themselves in a dilemma regarding the design and project planning of their production and assembly systems. Uncertainty in planning for the proper volume, for instance, continues to be one of the most significant challenges. E-mobility imposes certain requirements on the assembly process:
- top processing reliability for safety-related components
- high flexibility due to the wide variety of assemblies
- the use of system components with reliable electro-static discharge (ESD) capability
These components also require an assembly environment that both fulfills the guidelines of technical cleanliness and scores highly on the ergonomic front. Ultimately, the customer may face difficulties in coming up with an economical solution to all this complexity.
Fortunately, as an automation specialist, DEPRAG can address this complexity by offering flexible assembly solutions that can all be adapted to the current market situation, from components and manual workstations, up to semi- or fully automatic assembly systems. This flexibility helps mitigate production planning uncertainties and is responsive to the modification demands placed on production equipment. As one such solution, the “intelligent manual workstation” can be flexibly adjusted to any economic situation and is particularly beneficial if ROI does not allow a case to be made for full automation. This is especially relevant for E-mobility where production rate trends are difficult to predict. For the assembly of E-mobility components, it could be preferable to opt for a flexible, upgradeable assembly line with intelligent manual workstations that combine manual handling with high processing reliability.
In addition to its standardized manual workstations, DEPRAG has developed automated, extremely flexible assembly cells – the DCAM product family. Equipped with one or more modern screwdriving function modules, high-quality industrial spindle screwdrivers, and an appropriate screw feeder, it will complete any screwdriving task. The modular assembly cell is particularly suitable for fluctuating production rates, diverse product ranges, and short product life cycles. As a system solution, the DCAM combines efficiency with the best possible processing reliability.
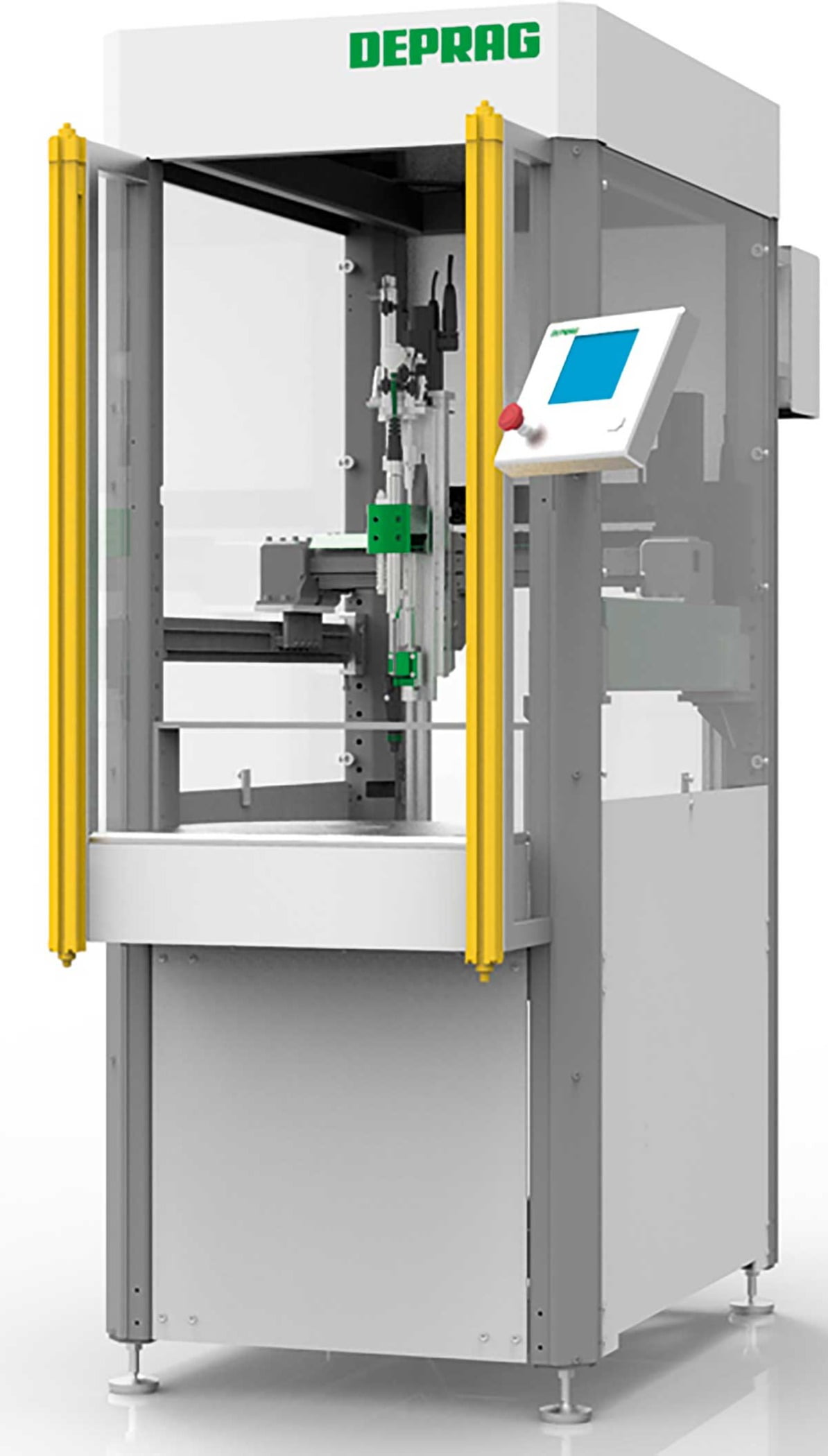