ASSEMBLY ESSENTIALS
Effective Tooling for Assembly Automation
Improving Cycle Time – Faster machine cycles are being driven to increase the throughput of finished products. Mechanical actuators in an automated assembly machine can influence a shortened cycle through responding more quickly to commands or simply by moving faster. Newer electric driven products can help by doing both. Electric signals travel faster than compressed air through tubing, and motor technology such as linear motors may increase controlled speeds and accelerations/decelerations. Do not discount pneumatic products though. For example, high speed point-of-use pneumatic valves are often extremely effective for speed when mounted directly at gripper.
Reorientation of Workpieces – Products being assembled often need to be accessed from every side. To gain access, parts may need to be flipped, rotated, or moved as they travel through an automated assembly process. This can sometimes be accomplished using a robot and a gripper, but physical interferences can get in the way. Stand-alone workpiece reorientation stations can be easily constructed from standard gripping, rotating, and linear components all pre-designed to mount and work together. Custom solutions are sometimes employed within gripper finger tooling to rotate workpieces while captured in the gripper fingers and being transported by a robot all in one step.
Planning for Change – Criteria for automated assembly machines can change over the course of its service life. Workpieces themselves may be updated, or new services or tasks may need to be implemented. To prepare for the future, consider modularity when choosing componentry to build a machine. For examples: If the gripper force requirement is higher than expected, will there be a way to increase/decrease it later? If rotation or linear positioning requirements change, can the devices be adjusted or replaced easily?
The bottom line is that you do not need to reinvent the wheel for every aspect of custom automation equipment. Standardized solutions are available from component manufacturing experts who are eager to help.
Courtesy of Steven Douglas Corp.
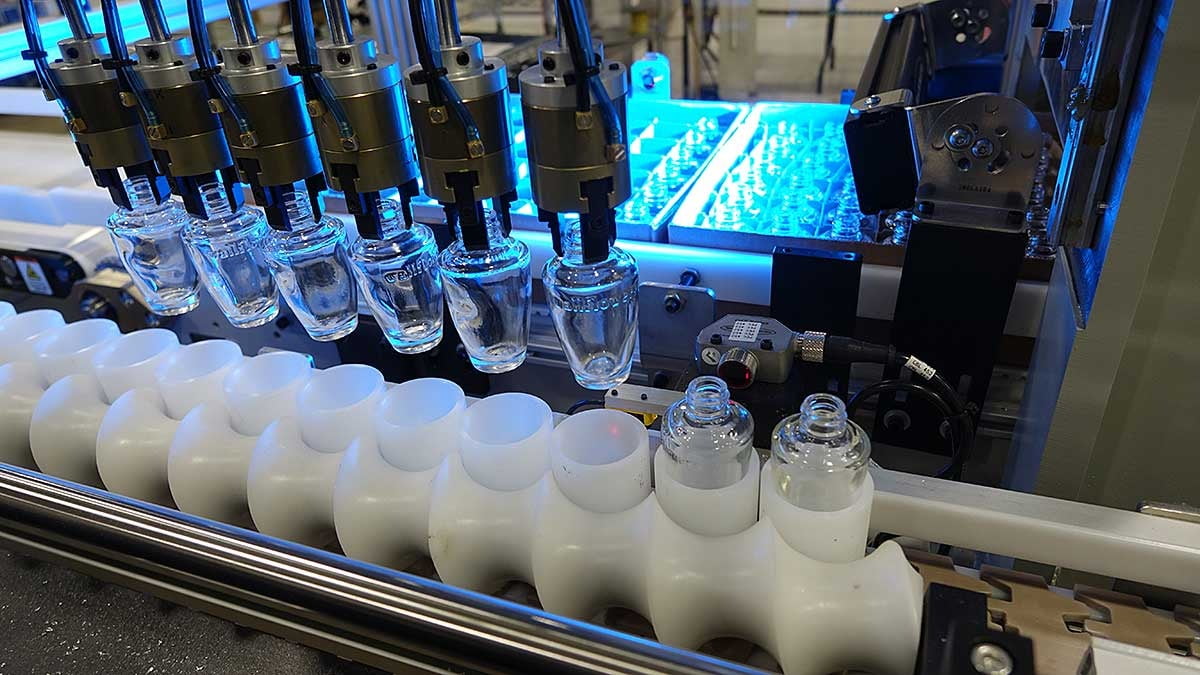
Assembly tasks often present difficult challenges to engineers when designing automated machinery. A variety of workpiece components from the size of tiny circuit board elements to automotive transmissions and beyond are typically fed through multiple processes such as parts insertion, joining/welding, marking, testing and more. Workpieces are typically fixed to pallets or nests to maintain strict orientation at every process. Each process is often served by a robot or other motion system. With so much happening in a small space where fast cycle times are important, and a high-quality finished product is paramount, machine engineering work can be overwhelming. The good news is that many automation-component manufactures have developed proven pre-engineered solutions that save time and costs of developing assembly machinery, while increasing their reliability. Some of these components are outlined here as an answer to common challenges.
Utilizing Robot Payload – Robots and pick-and-place systems are often a critical part of assembly tasks. They can take up valuable space and may be pushed to their limits in terms of maximizing speed and payload in their smallest possible size. End of Arm Tools (EOATs) should also be optimized allowing robots to operate at their top effectiveness. This is especially true in assembly operations where multiple grippers are routinely utilized to handle several parts at once. This is illustrated in the picture from Steven Douglas Corp. It is important to work with companies that have a variety of different standard gripping
solutions overlapping the same workpiece size range. Gripper mass, size, finger travel and force are developed together to produce families of grippers suited for specific jobs. At the same time, it is important to work with partners that understand finger tooling design. Gripper fingers that are well suited to their payload contribute to system reliability and can even produce better assembled products.
Flexibility and Multitasking – As new organizations begin automating for the first time, there is an increasing trend towards lower volume / high mix production. To answer the call of flexibility, there is a wealth of available quick-change products allowing tools to be replaced easily at robot wrists, machine tables, and even localized tooling like gripper fingers. Quick change devices can be deployed manually by machine operators or built into the automation system with robots or other devices automatically changing and storing tools for transforming tasks. Robots themselves can even be more easily redeployed as daily jobs vary.
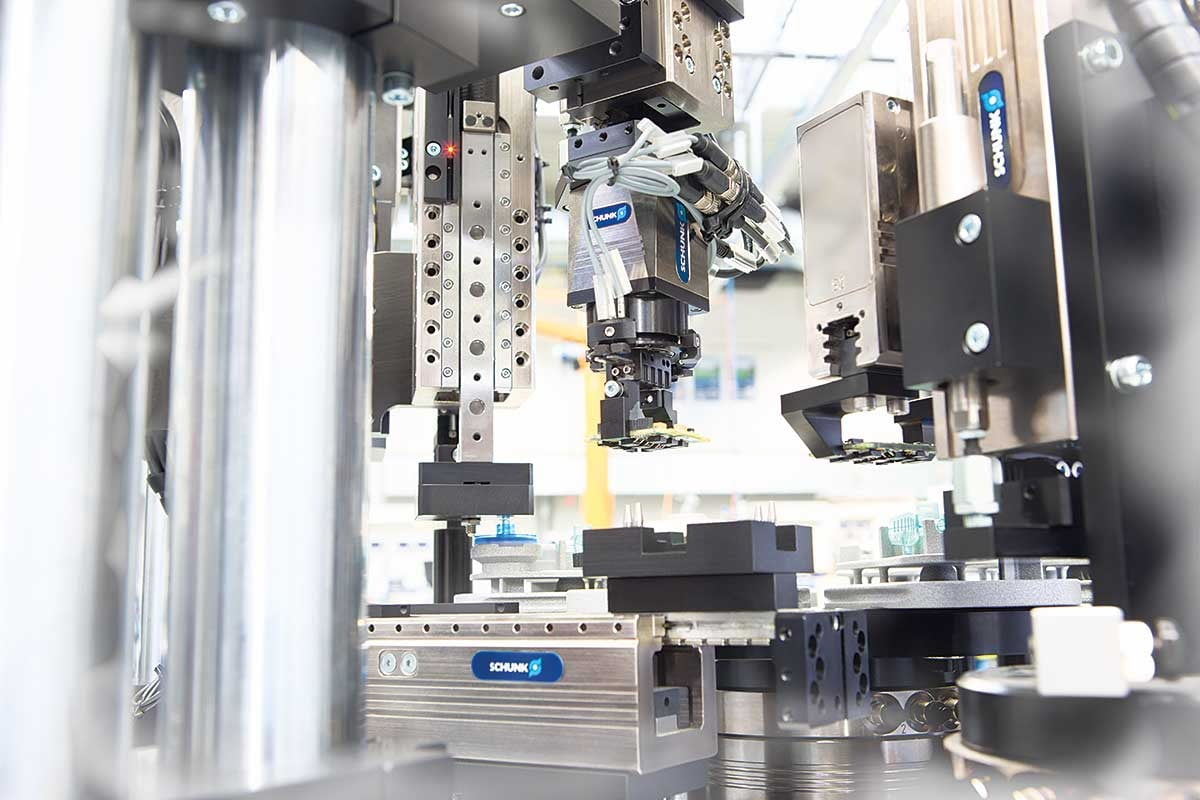
Example of high speed assembly application using all electric actuators