Plastic and Metal Welding
Labor shortages are driving new demand for automation.
Options for Screwfeeding
The Cobot Welder includes a versatile mobile welding table to perform welds on a variety of workpieces. Photo courtesy Hirebotics
A collaborative robot boosts capacity at a small manufacturer of metal brackets.
Cobot Welder
Transforms Small Business
Daniel Adams // Sales Director // Hirebotics LLC // Nashville, TN
Based in Sheboygan, WI, Iron Supports makes brackets and corbels for granite countertops, shelves, cabinets and fireplace mantels. The company began in a garage, but soon blossomed into a bustling business.
As demand surged and calls for custom products grew louder, company management stood at a crossroads. If the company was to grow, it would have to automate. But, it faced a Catch 22. Finding skilled welders was becoming more difficult, but finding someone who could program conventional welding robots wasn’t easy, either.
“We needed something simple that everybody could use,” recalls Ryan Hansen, president of Iron Supports. “So when we were comparing welding robot systems or packages, [one of the things] we were looking for was simplicity.”
In its search for a welding robot system, Iron Supports prioritized simplicity, ease of use, and rapid deployment. Management visited trade shows, conducted extensive Google searches, and consulted with industry experts. Many systems required extensive programming knowledge and lengthy setup times. They needed a system that was ready to go and could be quickly integrated into their production line.
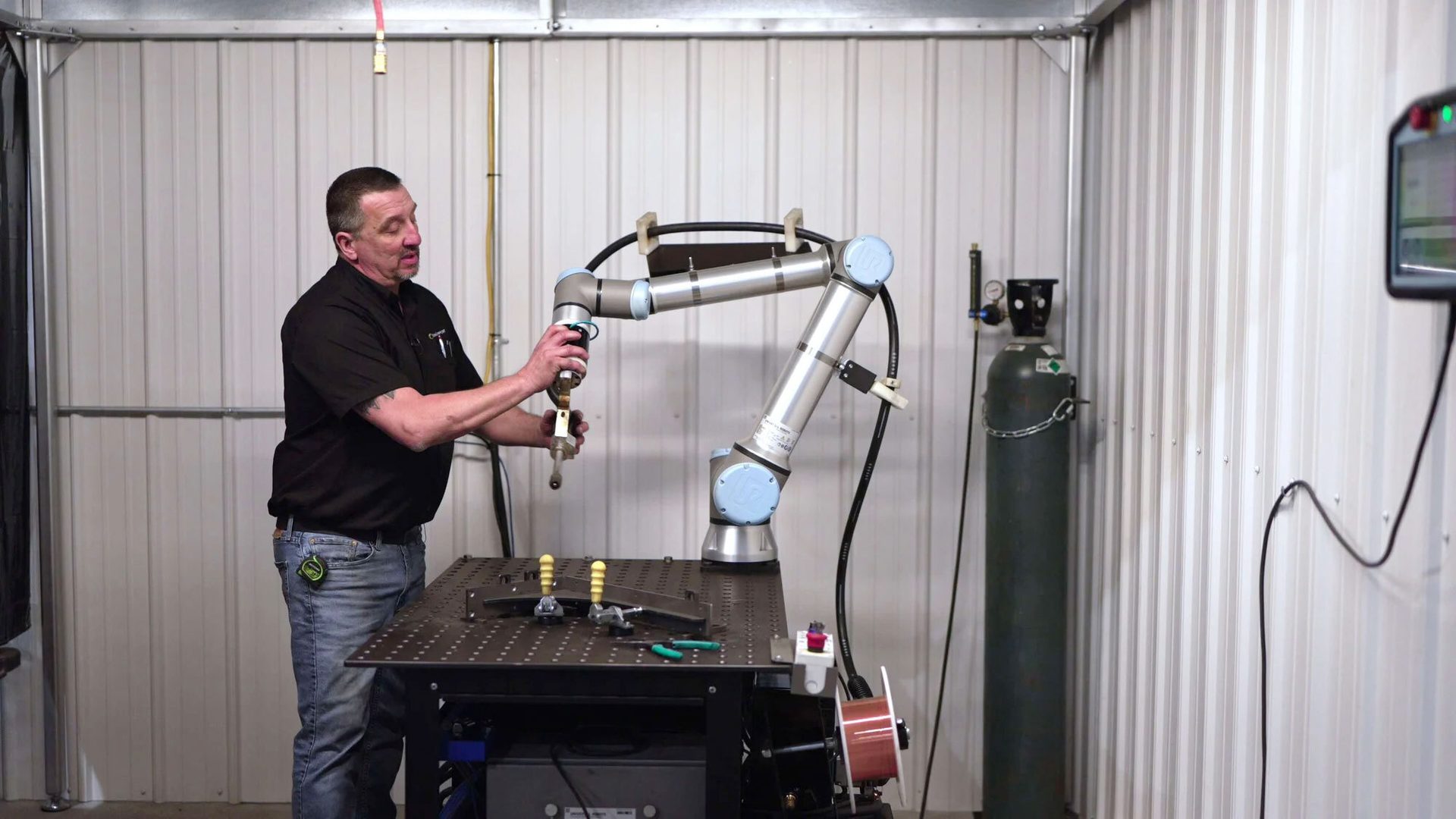
The cobot is programmed via Beacon, a smartphone app that uses plain shop language. Welders simply enter the parameters in the app and manually guide the cobot to each weld point. Photo courtesy Hirebotics
Iron Supports ultimately chose the Hirebotics Cobot Welder due to its user-friendly interface and quick availability. The system consists of a UR10e (51-inch reach) or UR20 (68.9-inch reach) collaborative robot from Universal Robots; a Miller Auto DeltaWeld 350 or ESAB Aristo 500iX with Robust Feed U82; a Tregaskiss Tough Gun MIG welding torch or an air-cooled Aristo RT Robotic Torch 72G; Hirebotics; Smart Puck for hands-on teaching; an operator panel with an emergency stop; and a versatile 48-by-32-inch mobile welding table to perform high-quality welds on a variety of workpieces.
The cobot is programmed via Beacon, a smartphone app that uses plain shop language. Beacon lets welders program the cobot in minutes. Welders simply enter the weld parameters in the app and manually guide the cobot. Beacon automatically populates the weld points by pressing the teach button. No teach pendant and specialist knowledge is required.
The Cobot Welder offered the capacity that Iron Supports needed and was ready to ship immediately, allowing for fast implementation.
“All I was looking for was a robot that could do a wide variety of things very quickly and easily, and it had to be ready to go,” says Hansen. “We didn’t want a six-month implementation. We just didn’t have that time. Hirebotics had these cells, with the capacity we were looking for, built and ready to ship.”
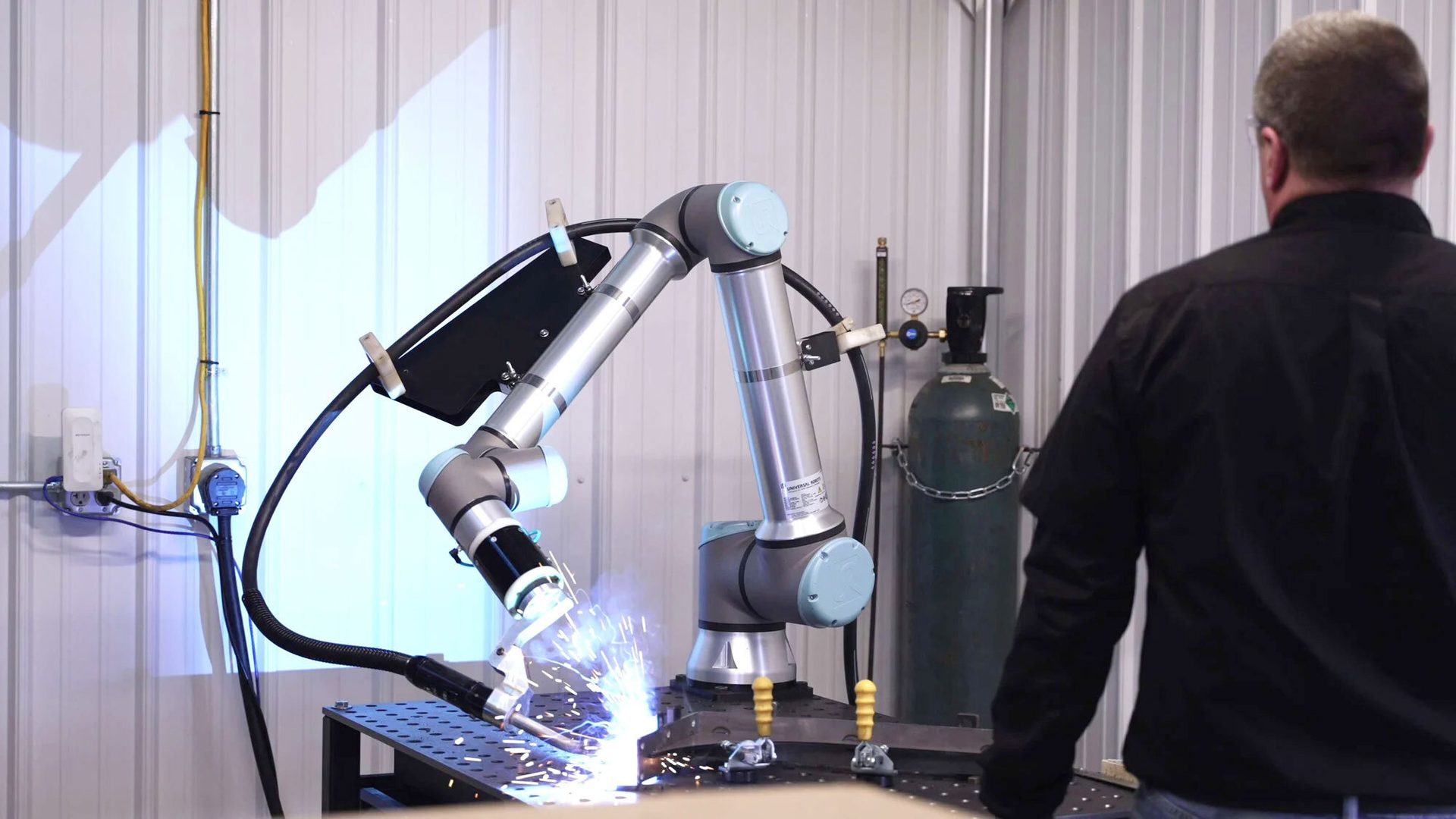
At Iron Supports, the Cobot Welder was fully operational within a week. Photo courtesy Hirebotics
Plug, Play, Produce
The Hirebotics Cobot Welder was delivered and operational within a week. The setup process was straightforward, enabling the team to begin production within hours of receiving the equipment. The first production run was completed successfully, demonstrating the system’s effectiveness and ease of use.
“We wired the money and had that thing up here in a week. We were literally using it in production within two days of plugging it in,” says Hansen.
“The day we received the cobot, it was the middle of the afternoon,” recalls Iron Supports’ shop manager. “By four or five o’clock, we had it running. It was operational. The next morning I came in after looking at some of the programming at night at home. And within, I would say, an hour, I was making welds.”
The integration of the Hirebotics Cobot Welder had a profound impact on Iron Supports’ operations. The cobot significantly boosted productivity, allowing the company to catch up on backlogged orders and handle new ones efficiently. The quality of the welds improved, leading to a reduction in scrap and rework.
Inspection System
“The impact the robot has had on our business productivity is pretty crazy,” says Hansen. “Realistically, we [went from] literally having to not take orders or cancel orders because we couldn’t keep up, to catching up with that backlog and working ahead.”
The ease of programming and reprogramming the cobot enabled Iron Supports to quickly adapt to new product lines. This flexibility was especially valuable given the company’s lack of a full-time programmer. The Beacon app also provides remote access and diagnostics, enhancing operational support.
“We can use the cobot to program and test [a new] fixture, make any changes to the fixture, come back in the same day, and reprogram [the cobot] immediately. Any one of the welders can do that,” says Hansen.
Overall, the Cobot Welder transformed Iron Supports’ production process, leading to higher productivity, better quality and increased capacity to handle orders. This technology has positioned the company for continued growth and success.
“As far as quality goes, it was night and day. You can only weld the same part in a fixture by hand perfectly so many times. I don’t have exact numbers, but I know that we have a lot less scrap now than we ever did,” says Hansen.
For more information on welding with cobots, visit www.hirebotics.com.
ASSEMBLY ONLINE
For more information on robotic welding, visit www.assemblymag.com to read these articles: