Assembly Presses
Labor shortages are driving new demand for automation.
Options for Screwfeeding
In the spring of 2022, the first press hardening line from AP&T was installed at Simwon’s factory in Kyle, TX. Photo courtesy AP&T
A turnkey automated line produces stampings for Tesla and other automotive OEMs.
Press Hardening Forms Strong, Lightweight Parts
John Sprovieri // Chief Editor
Press hardening technology has created new opportunities for producing lighter and more fuel-efficient vehicles.
During press hardening, boron steel blanks are heated to a temperature as high as 930 F, formed and cooled in a carefully controlled process. During the process, the steel’s molecular structure is transformed into ultra high strength steel (UHSS). The finished part is three times more stable than the original material, and it becomes extremely strong in relation to its weight.
The method also enables the manufacture of complex part shapes with high dimensional stability and a great deal of repeat accuracy in a quick and cost-efficient manner.
For automakers, increasing the use of press hardened body parts means that collision safety can be enhanced while reducing vehicle weight. A weight savings of 100 kilograms means that fuel consumption can be reduced by an average of 0.5 liters for every 100 kilometers driven. As a result, most OEMs have substantially increased their usage of press hardened parts. In some car models, some 20 to 40 percent of the weight of a body in white consists of press hardened materials.
Typical press hardened parts include the A and B pillars, the front and rear side members, cross-members and door rings.
Headquartered in Ulricehamn, Sweden, with a office in Monroe, NC, AP&T is one of the world’s leading suppliers of turnkey production lines for manufacturing press hardened vehicle parts. Since 2001, the company has installed more than 140 press hardening lines worldwide.
AP&T’s lines include all of the equipment to make press hardened parts, including presses, automation, tooling and furnace systems. The lines are put together from standardized modules are flexible, reliable and compact. For example, the company’s Multi-Layer Furnace allows several furnace modules to be stacked on top of each other, which means the installation is space-efficient. Production can also be scaled up or down based on need, and heating can be adjusted thereafter. Since the furnace only contains a few movable parts and the blanks are immobile during the heating process, the risk of downtime and damage to materials is reduced.
AP&T’s system for partial press hardening of structural parts, TemperBox, allows hard and soft zones to be combined in a single finished part, paving the way for innovative body designs and cost-efficient production. Individually defined areas of press hardened components can be fully hardened to maximize strength while other areas remain soft to achieve the desired ductility and to facilitate postprocessing, such as joining or mechanical cutting. This means engineers can work more freely without considering costly reinforcements or time-intensive hardening processes. TemperBox can be integrated with AP&T’s Multi-Layer Furnaces, as well as be combined with any other type of heat treatment equipment.
AP&T’s in-line process monitoring system enables an optimized and well-controlled press hardening process, which ensures the formed part has a high and consistent level of quality. In addition, cycle times can be reduced. Pyrometers and infrared cameras are used to measure the material’s temperature with a high degree of precision before and after pressing. The pyrometer registers the absolute temperature at a certain point, while the infrared cameras read the heat distribution on the part’s surface. All of this takes place without any of the equipment coming into physical contact with the material.
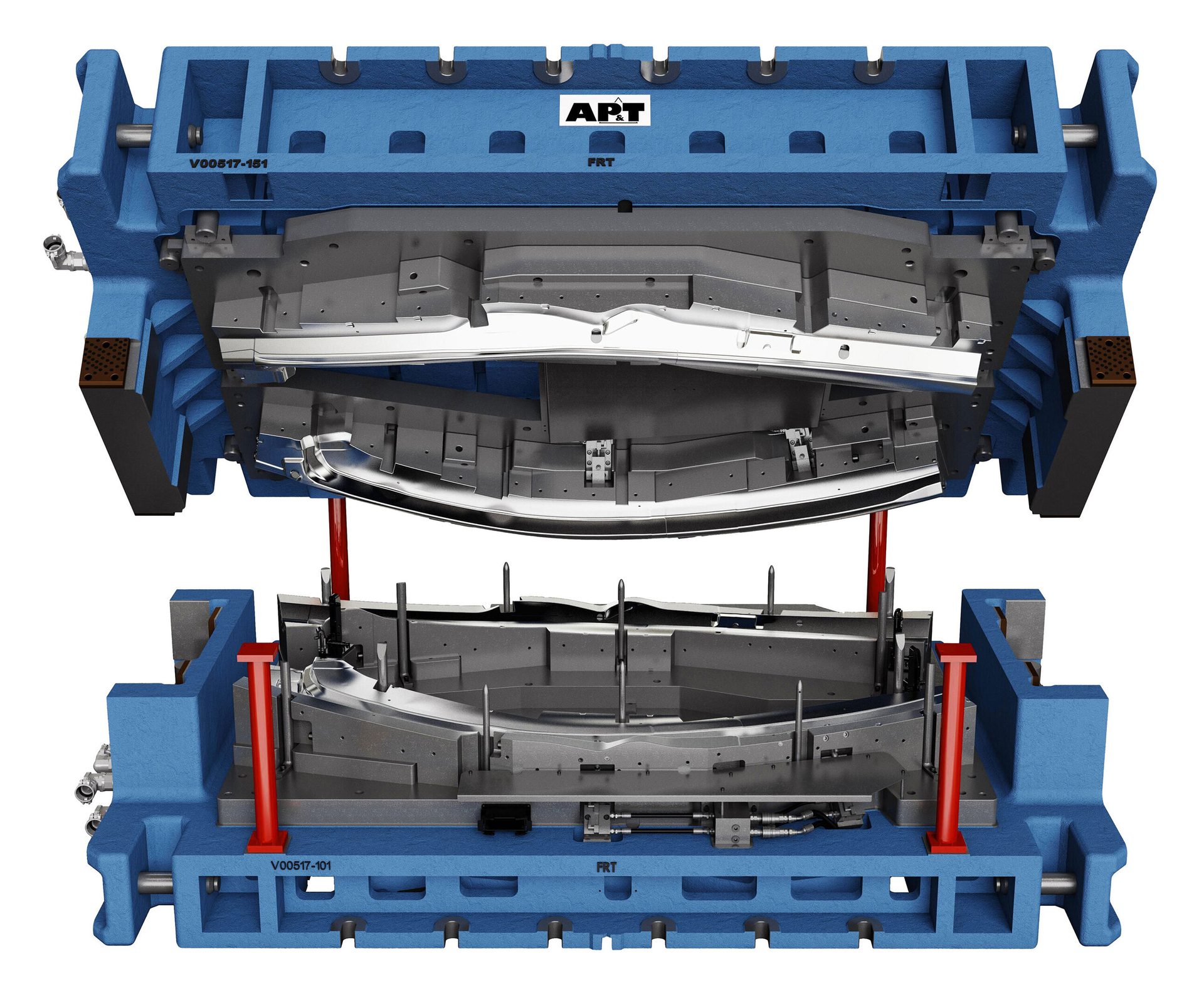
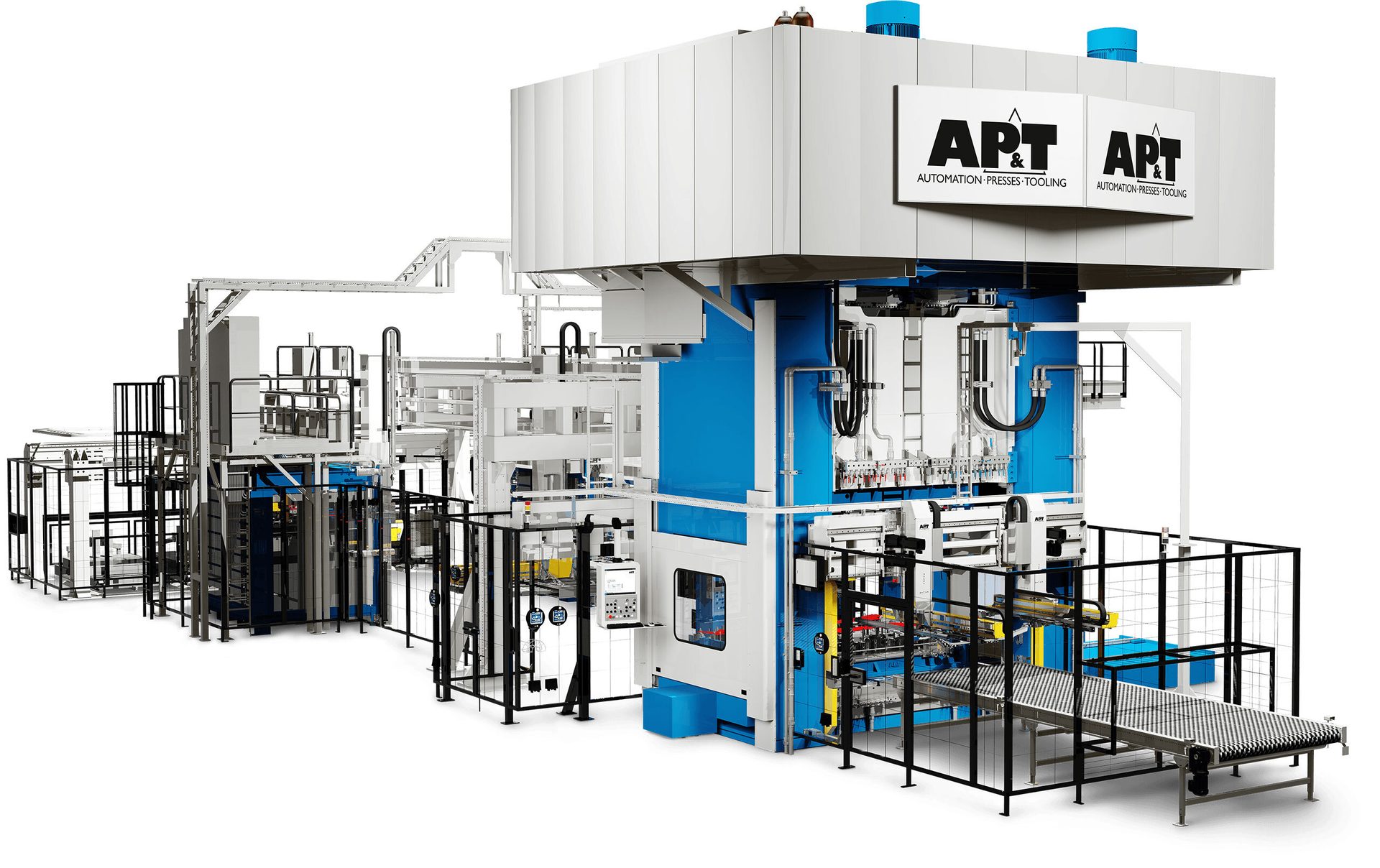
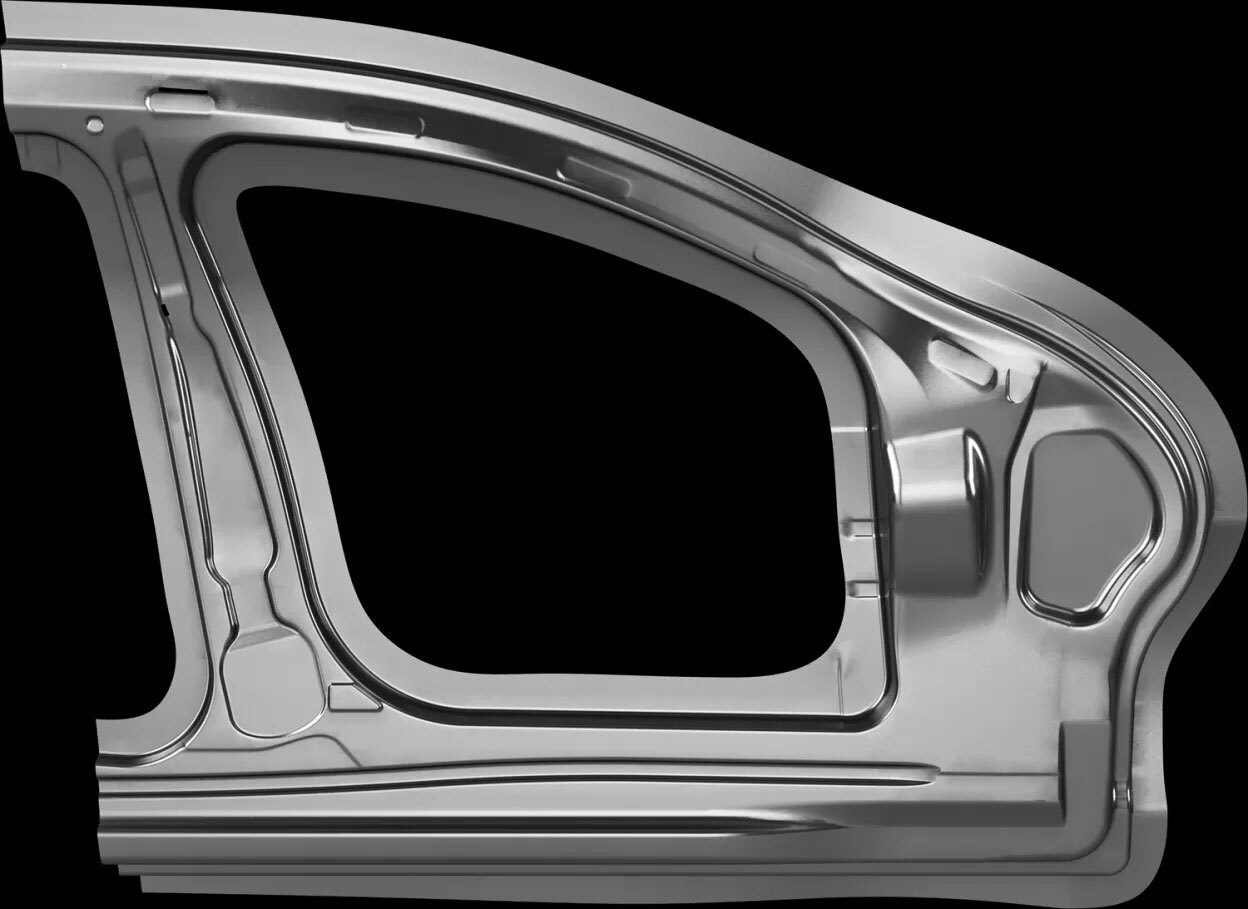
A Press Hardening Line in Texas
Based in Anyang, South Korea, Simwon Tech is a leading manufacturer of automotive sheet-metal stampings and assemblies, including door modules, floor modules, sunroofs and frame components. Founded in 2006, the company operates eight facilities worldwide and tallied more than $1.14 billion in sales last year.
AP&T has spent many years building up a relationship with Simwon and its parent company, MS Autotech Co. Ltd. in South Korea. During a visit to China a few years ago, Simwon’s managing director got the opportunity to see how AP&T’s press-hardening production lines perform in action. It was the start of a rewarding collaboration between the two parties.
In the spring of 2022, the first press hardening line from AP&T was installed at Simwon’s factory in Kyle, TX, which produces metal stampings and assemblies for Tesla and other OEMs.
“The new line is primarily used to manufacture door rings for one of our larger American customers,” says Jeon Incheol, senior manager of the overseas sales team at Simwon Co Ltd. “To meet their needs, the technology has to run faultlessly, and we need to be able to produce at top speed. AP&T’s line has exceeded our high expectations. The output is between 15 and 20 percent higher than our other press hardening lines.”
“We are naturally pleased to fulfill Simwon’s high requirements on product quality, cycle times and machine availability,” adds Peter Robisch, sales manager at AP&T. “For us, this is a strategically important deal that has strengthened our position in press hardening on the North American market.”
Now that the line has been running for close to a year and a half, both companies are prepared to discuss how they can deepen their collaboration.
“In this context, it’s a great advantage that we have well-established service, support, spare part supply and sales organizations in the U.S.,” says Robisch.
The modular line includes a hydraulic press with a press force of 1,200 tons, automation equipment and a control system. Thanks to the uniform control system, the line’s hydraulic presses and linear robots can be synchronized, providing an optimal process and short cycle times. The line is also equipped with AP&T’s in-line process monitoring. Its cameras and pyrometers ensure a well-controlled manufacturing process and a high, even quality of produced parts.
To learn more about press hardening equipment, visit the company’s website at www.aptgroup.com.